Let’s explore the pillars of a streamlined assembly process and how cutting-edge tools and technologies can elevate your sheet metal components to unmatched levels of precision and reliability.
Reliable and durable sheet metal assemblies rely heavily on sheet metal parts fabricated with precision and efficiency in mind.
Streamlining the process of sheet metal assembly, where accuracy and repeatability foster the fabrication of intricate and complex sheet metal components, is essential when serving leading manufacturers in today’s most important industries.
Streamlining contributes to enhancements in efficiency, product quality, and consistency regardless of the intricacy of the design. Projects also benefit from reduced lead times, lower production costs, and minimized waste.
The key is to find a trusted metal manufacturer with an expert assembly team and an established process renowned for reliability and precision.
Pinnacle Precision is that manufacturer. For more than 50 years, our crew has built expertise in sheet metal fabrication and assembly, delivering perfect fit and function every time.
As a total assembly sheet metal manufacturer, we take a team-forward, solutions-first mentality that’s earned the trust of customers from leading medical, aerospace, information and communications technology, energy, and entertainment companies.
This article explores the importance of a streamlined process in sheet metal assembly, the pillars of streamlining, and the tools and technologies for streamlining sheet metal assemblies.
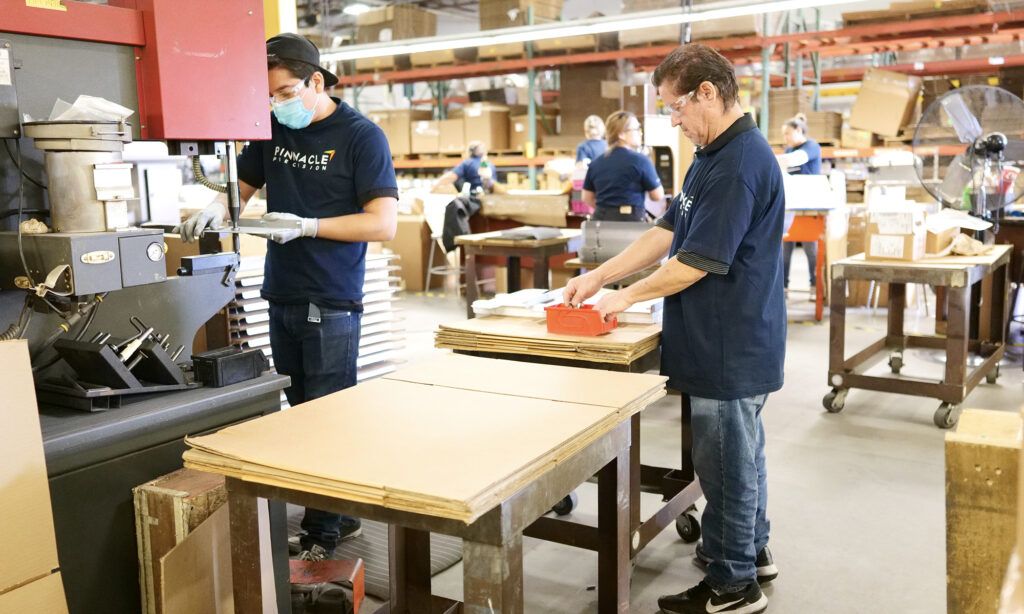
The Essentials of Streamlined Sheet Metal Assembly
Sheet Metal Assembly is a fundamental part of precision metal manufacturing, where individual sheet metal components are meticulously joined together to create a final, functional product. It involves various techniques, including welding, fastening, and riveting, all used to assemble custom components with exceptional accuracy.
Ideal for industries where precision is paramount, like automotive, aerospace, and electronics, sheet metal assembly delivers robust and seamless metal components that can withstand the demands of their intended applications in even the harshest environments.
With even the slightest deviation in assembly leading to reduced product quality and performance, it is essential that your assembly process and team of assemblers ensure that every piece fits together flawlessly and performs its intended function with utmost efficiency and durability.
Delivering Precise Sheet Metal Parts: The Pillars of Streamlining
In precision metal manufacturing, streamlining the assembly process relies on five essential pillars: efficiency, accuracy, scalability, flexibility and cost-effectiveness.
Efficiency:
Efficiency ensures that operations are optimized, minimizing waste, and reducing production time, which ultimately leads to cost savings.
Accuracy:
Accuracy is the cornerstone of quality assurance, ensuring that each component aligns perfectly with specifications and standards.
Scalability:
Scalability is crucial for adapting to changing production demands, enabling manufacturers to expand or contract their operations as needed.
Flexibility:
Flexibility is the key to handling custom orders and accommodating design variations, allowing manufacturers to respond to the dynamic needs of the market.
Cost-effectiveness:
Cost-effectiveness is central to maintaining a competitive edge, as efficient processes translate into reduced production costs.
These five pillars together form a robust foundation for a streamlined sheet metal assembly process, balancing the precision and productivity required to meet the demands of the modern manufacturing landscape.
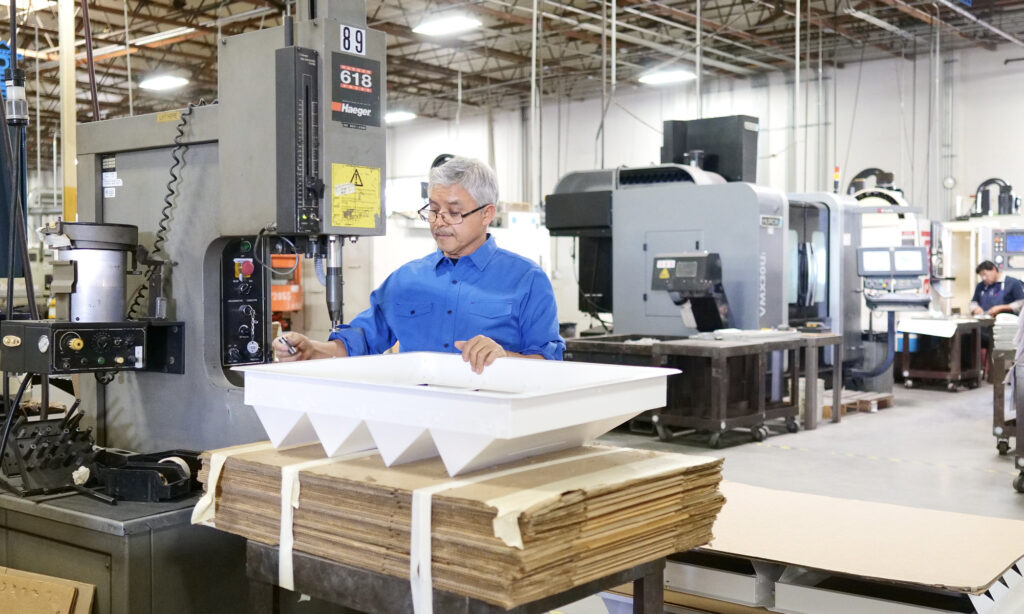
The Role of Precision in Streamlining Mechanical Assembly
When considering precision’s role in streamlining processes, you must first consider the cost of inefficiency. Small errors in the assembly process can snowball into significant problems, both in terms of cost and product quality. A minor misalignment or an imprecise weld can compromise the structural integrity of the final product, potentially leading to costly rework, scrap, or even product failures in the field.
Inefficient assembly methods can also result in longer lead times, increased labor costs, and increased material waste – impacting both your bottom line and reputation.
Let’s look at an example of Ventilator Manufacturing for The Medical industry.
When you’re producing ventilators for use in intensive care units, they must be delivered with exact precision in order to meet stringent medical grade standards. Now, during assembly, imagine an incorrect cut is made to the ventilator components. This would result in it immediately failing quality assurance tests. But, the ripple effect goes much further. Not only does it risk a delay to production in an industry that can’t afford to wait, but it also presents unforeseen costs of potential reworks and delays… not to mention the potential risk an error like that poses to patient lives.
The Power of Process in Sheet Metal Assembly
In precision metal manufacturing, a structured, streamlined assembly process ensures consistent performance and efficiency. With a streamlined process in place, you will have clear guidelines for each step, from material preparation to final inspection, reducing errors and variations. This not only enhances the overall product quality but also minimizes waste, reduces production costs, and shortens lead times.
With a well-defined, streamlined process, intricate, high-tolerance sheet metal components can be produced with unwavering precision.
To meet the highest functional standards, Pinnacle considers every aspect of the final product, including everything connected to it. We match material tolerances and component alignments to ensure that every piece fits together flawlessly and performs its intended function with utmost efficiency and durability.
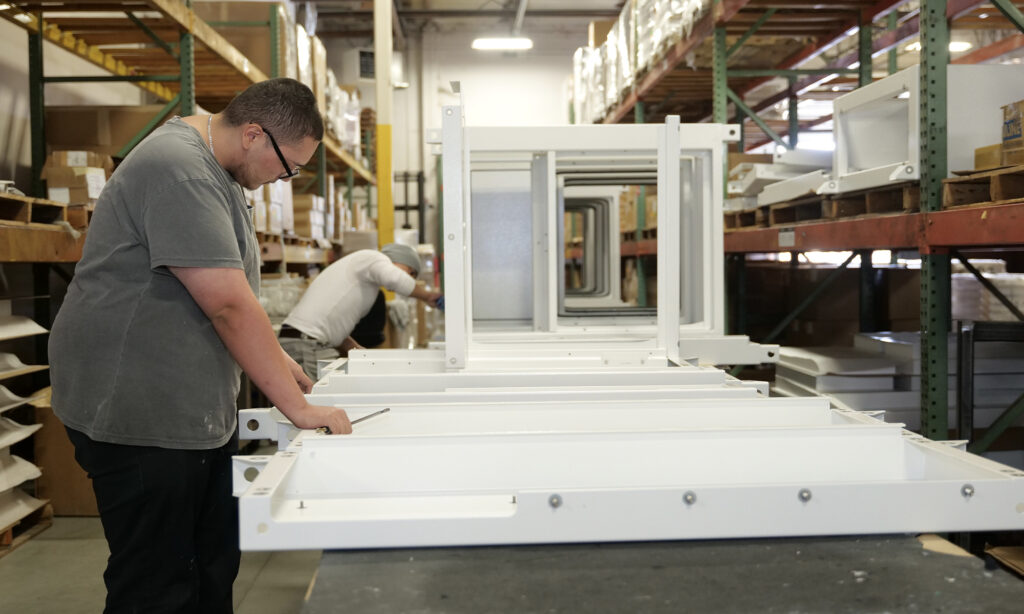
The Pinnacle process
Here at Pinnacle, precision starts with our process. Each project that comes into our Southern California headquarters receives the highest level of attention. Our Customer Support team excels in translating customer needs into actionable plans for our Technical, Production, and Quality Assurance teams.
Our manufacturing experts utilize CNC laser cutting and punch presses for precise sheets that are then delivered to our machining, forming, welding, and finishing departments. From there, we help our customers with assembly, hardware installation, and seal applications before our quality assurance team carefully looks at the final product.
Our proven process includes:
Component Fabrication: We fabricate each individual sheet metal component using a variety of techniques, including cutting, bending, punching, milling, turning, and welding.
Quality Control: We carefully inspect each component to ensure it meets exacting quality standards and specifications.
Assembly: The individual components are then assembled together using welding, fasteners, adhesives, or other suitable methods. The assembly process requires precise alignment and fit to ensure the final product’s structural integrity and functionality.
Finishing: To enhance the appearance and protect the product against corrosion, finishing touches such as painting, coating, or polishing may be applied after assembly.
Quality Assurance: To ensure that the final assembled product meets all safety and design specifications, it undergoes rigorous quality assurance checks.
Tools and Technologies for Streamlined Processes
The use of cutting-edge tools and technologies is essential to achieving a streamlined assembly process in precision metal manufacturing. Computer-aided design (CAD) software allows component modeling and planning, CNC machining centers allow for precise cutting and shaping, robotic welders make joining consistent and efficient, and quality control systems such as laser measurement and 3D scanning make meticulous inspections possible. Material flow and inventory control are also enhanced by automated conveyors, material handling systems, and inventory management software.
Achieving high-quality, cost-effective assembly environments with such technology not only boosts productivity and accuracy but also ensures consistency and efficiency in every aspect of sheet metal assembly.
At Pinnacle, we help customers across the renewable energy, medical, and aerospace industries through our streamlined sheet metal assembly.
To ensure exactness and precision, assemblies are performed using semi-automatic presses, automatic presses with auto feeds, and hardware presses with auto feeds.
Our class-leading tools include:
(9) Semi-Automatic Presses for threaded fastener installations
(6) Auto-Presses with auto feeds
(2) Hardware Presses with auto feeds
The Pinnacle Advantage - Masters of Mechanical Assembly
Pinnacle Precision manufactures multiple parts for the world’s most advanced and vital industries, including electronic parts and custom components for use in medical, aerospace, information & communications, renewable energy, and entertainment. Our advanced approach to every capability means that the finished product can withstand the harshest environments and look good year after year.
Our expert team of metal assembly masters use a variety of tools and techniques to achieve flawless functionality, structural integrity, and dimensional accuracy while also meeting stringent quality standards.
As proven experts in assembling metal parts, we are prepared to take on any challenge that helps speed up the time it takes for you to get a part into production. With unmatched expertise, machines, and tooling, we deliver exactness and precision in applying various seals and installing hardware.
Let’s talk about your most demanding metal fabrication requirements. Contact us today.