Explore the role that precision metal fabrication plays in the aerospace sector, the stringent industry standards and regulations that govern manufacturing, and showcase how precision metal fabrication is shaping the future of the aerospace industry.
In an industry where the slightest error can be the difference between life and death, it’s little wonder why precision metal fabrication in aerospace is nothing short of paramount.
With stringent industry standards and regulations to ensure the utmost safety and reliability in aviation, precision metal fabrication is blending innovation with compliance to develop cutting-edge aircraft, spacecraft, and aerospace technologies.
As one of the leading aerospace fabrication companies, Pinnacle Precision has a reputation for consistently delivering precision sheet metal parts for a range of aerospace applications.
A trusted supplier of precision metal components to leading industrial manufacturers, Pinnacle’s decades of aerospace metal fabrication services experience have honed its ability to consistently deliver top-notch, punctual parts that meet and exceed the rigorous standards of the aerospace sector.
In this article, we explore the critical role that precision metal fabrication plays in the aerospace sector, the stringent industry standards and regulations that govern manufacturing, and showcase how precision metal fabrication is shaping the future of the aerospace industry.
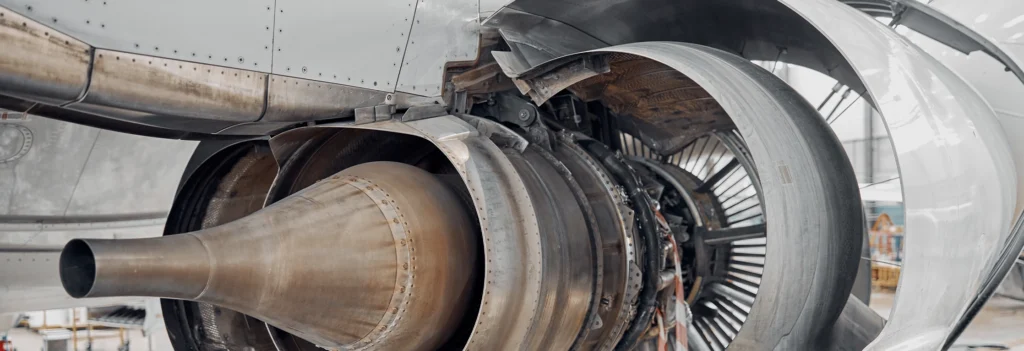
The Art of Aerospace Metal Fabrication
Aerospace metal fabrication is a specialized branch of metal manufacturing that focuses on producing components and structures for the aerospace industry. It involves precisely shaping, cutting, and assembling metallic materials for aerospace and aviation parts.
Responsible for improving aerospace vehicles’ performance, safety, and efficiency, it involves using advanced tools and techniques, like laser cutting and photochemical etching, to manufacture parts for everything from aircraft frames to engine components, avionics systems, and other crucial elements.
Precision is paramount in aerospace sheet metal fabrication, as the intricate components must adhere to strict tolerances and quality standards to ensure the structural integrity and reliability of the final products.
Ensuring Safety and Reliability through Compliance
In precision metal manufacturing for aerospace, compliance plays a pivotal role in ensuring safety, reliability, and overall adherence to industry standards.
The aerospace sector is highly regulated, with stringent quality and safety standards to guarantee the integrity of components used in aircraft and spacecraft. Adhering to compliance standards involves meticulous attention to detail in design, fabrication, and testing processes. This commitment to compliance ensures that each component meets the specified requirements and contributes to the overall safety and reliability of aerospace vehicles.
Strict adherence to regulations helps prevent potential failures, enhances the longevity of components, and ultimately plays a critical role in maintaining the high standards demanded by the aerospace industry for the safety of passengers and the success of missions.
Compliance with the following regulations is essential to maintain aerospace component safety and reliability:
FAA (Federal Aviation Administration)
- FAR (Federal Aviation Regulations) govern civil aviation in the U.S., covering certification, materials, quality management, design, and safety testing.
- AS (Aerospace Standard) and AMS (Aerospace Material Specification) provide industry-specific standards.
- Stringent quality management systems and safety certifications are required.
EASA (European Union Aviation Safety Agency)
- EASA Part 21 outlines certification requirements for aircraft and components.
- Certification Specifications (CS) specify technical and safety requirements.
- EASA Part 145 covers maintenance and repair.
- Production Organization Approvals (POA) ensure production process compliance.
- Regulations also address continuing airworthiness and environmental standards.
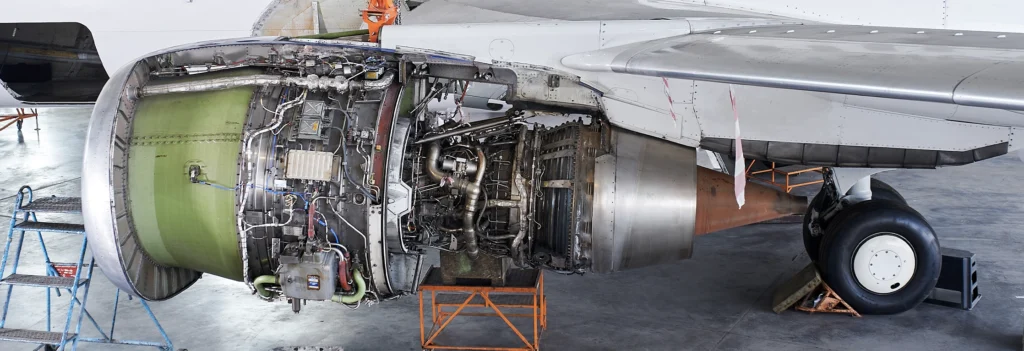
The Importance of Material Selection in Aerospace Applications
The material selected for aerospace applications is a critical decision as it directly influences aircraft and spacecraft performance, durability, and safety.
The chosen materials, often alloys like aluminum sheet metal selected for their corrosion resistance, play a crucial role in enhancing the longevity and reliability of aerospace components.
Choosing the right materials for aerospace sheet metal parts requires balancing strength and weight and ensuring resistance to environmental factors, fatigue, and corrosion. It is also important for materials to have predictable thermal expansion, electrical conductivity, and compatibility with manufacturing processes. For certain applications, carbon steel can be used.
Material choices are also influenced by cost and availability.
The Tools and Techniques Used in Aerospace Sheet Metal Fabrication
In an industry where precision and reliability are essential, a number of advanced tools and techniques are relied upon during the fabrication process.
Precision metal fabrication techniques such as CNC machining, laser cutting, and 3D printing are vital in aerospace manufacturing due to their accuracy and versatility.
CNC machining ensures tight tolerances and batch production, while laser cutting offers speed and reduced material waste. 3D printing allows for complex geometries, lightweight structures, rapid prototyping, and customization, all of which are essential for innovation and efficiency in the aerospace industry.
At Pinnacle, we boast several CNC-powered multi-axis mills that produce sheet metal parts and metal components to the tightest tolerances used by leading aerospace companies. Our Technical and Production professionals leverage their experience and expertise to deliver precise parts that last.
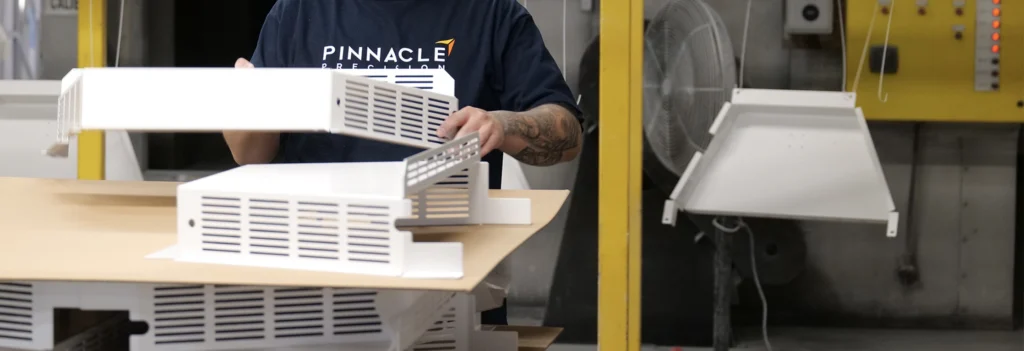
Ensuring Excellence through Quality Control and Finishing
Aerospace metal fabrication is subject to stringent quality control procedures to ensure compliance with industry standards. As part of these procedures, materials are inspected, dimensions are checked, nondestructive testing is performed, and documentation is comprehensive. Key components include material traceability, compliance with aerospace standards, and regulatory oversight.
Assuring safety and reliability of aerospace components is maintained through continuous improvement through data analysis and supplier audits.
Finishing processes in aerospace metal fabrication play an equally critical role in delivering high-quality, performance-ready components. Impeccable finishing processes are essential for achieving the exceptional quality, longevity, and safety required in this demanding industry. These processes include surface treatments, coatings, and inspections that ensure the final product meets aerospace standards.
Surface treatments, such as anodizing or passivation, provide corrosion resistance and enhance durability, crucial for aerospace components exposed to harsh environmental conditions. Protective coatings offer added resilience and can improve thermal performance or reduce radar signatures in military applications.
Precision and reliability of the finished component are assured by rigorous inspections, including dimensional checks and non-destructive tests.
At Pinnacle, we ensure excellence in everything we do.
Fabricating and finishing are the first steps in delivering accurate assemblies, parts, and components. Our Quality Assurance team reviews customer requirements, monitors the manufacturing processes, and inspects projects for accuracy and durability using laser, digital, and dial tools.
We aim to exceed industry standards and customer expectations while delivering essential parts at just the right time. Our Quality Assurance motto is “Quality people make quality parts,” so the team empowers every employee to act as a Quality Control expert in their department and performs regular training sessions. Pinnacle’s Quality Assurance team establishes and maintains our procedures to comply with ITAR, ISO9001:2015, AS9100D, and RoHS certifications.

The Pinnacle Precision Advantage
Pinnacle Precision boasts decades of experience delivering a new level of precision to industry-leading companies within the aerospace industry.
Pinnacle is an AS9100-certified manufacturer of precision metal components used in the aerospace industry, which is no easy feat. To earn the AS9100 certification, Pinnacle’s team met stringent manufacturing and quality management standards developed by the Society of Automotive Engineers and stands ready to support aerospace customers’ needs. Pinnacle leverages its decades of experience to deliver precision components for applications from cabin to cargo.
We have expertise working with aerospace-grade alloys, finishes, and hardening requirements to support leading aerospace manufacturers.
One thing that sets Pinnacle apart from other metal fabrication companies is the level of expertise on our production floor. Many of our team members have decades of fabrication experience and understand the importance of accuracy and precision.
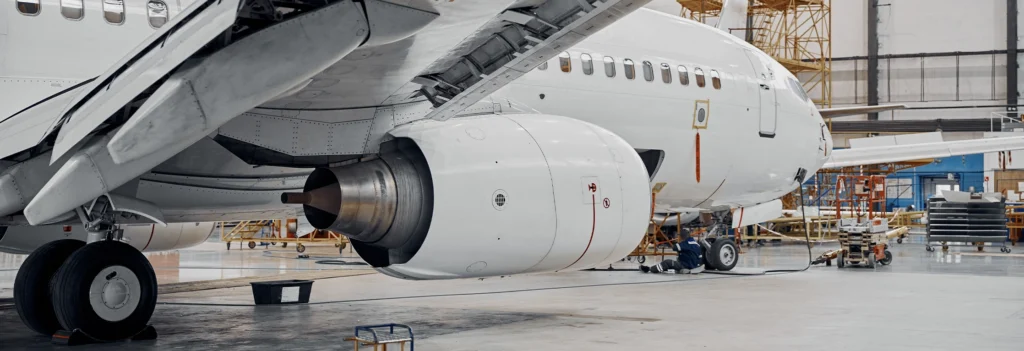
The Future of Aerospace Sheet Metal Forming
As aerospace engineering evolves, the demand for lighter, more durable, and highly efficient materials will fuel developments in precision metal manufacturing.
In the coming years, emerging technologies, such as additive manufacturing and smart materials, will revolutionize the industry, offering new opportunities for intricate designs and greater performance. Precision will continue to be the linchpin, ensuring that aerospace components meet the rigorous standards of safety, reliability, and efficiency essential for the next generation of aircraft and spacecraft.
As specialists in sheet metal aerospace components, the team at Pinnacle can deliver the highest level of precision for your aerospace project.
Talk to us today for precision and innovation in aerospace sheet metal fabrication services.