We look at the tools needed to produce complex precision parts and components and the remarkable advantages of high-speed machining to leading industries worldwide.
In the ever-evolving world of precision metal manufacturing, the latest technologies, like 5-axis CNC machining centers, are essential when producing metal parts and components. Adding CNC machines to plant floors expands what’s possible in metal component production.
Five-axis machining centers are at the heart of modern manufacturing plants. Unlike its 3-axis counterpart, which limits the movement of a cutting tool, this advanced machining process moves along five different linear axes simultaneously, enabling complex geometries and intricate operations on a wide range of materials. Five-axis machines can tilt and rotate its cutting tool, providing a level of freedom that opens up a world of possibilities for intricate, multi-dimensional, and high-precision machining.
As a full-service metal solutions provider, Pinnacle Precision leverages a suite of CNC-powered machines to produce complex and intricate parts and components for the world’s most advanced and vital industries, including medical, aerospace, information & communications, energy, and entertainment.
In November 2023, Pinnacle integrated two DN Solutions SVM 5100L vertical machining centers and a Lynx 2100LY turning center to the center’s 73,000-square-foot facility. The SVM series boosts productivity by reducing the acceleration and deceleration rates for the spindle and axis drives and reducing retooling times between jobs. Lynx enables the machining of reliable complex parts in a single setup thanks to the Y-axis and sub-spindle.
By continuing to invest in state-of-the-art machinery and employee training, we’re answering customer calls for full-service metal solutions, including parts, components, and assemblies that can withstand the harshest environments.
In this article, we look at the tools needed to produce complex precision parts and components, especially 5-axis CNC machines, how these machines work, and the remarkable advantages this high-speed machining brings to leading industries right across the globe.
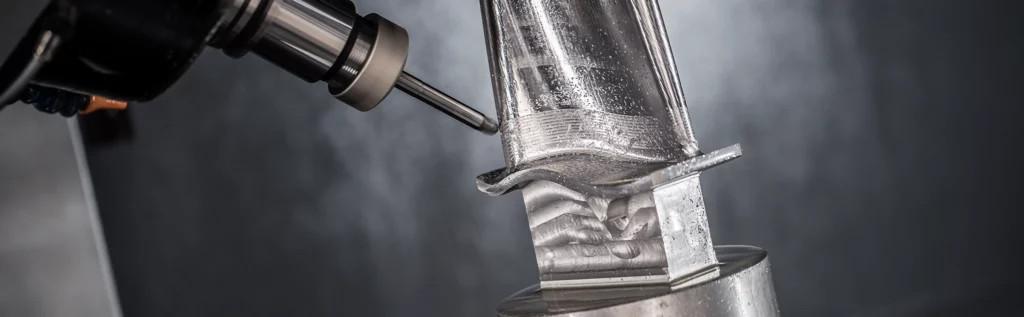
What is five-axis machining?
Five-axis machining is a cutting-edge approach that redefines the production of complex parts and components in precision metal manufacturing.
Widely embraced in manufacturing and machining industries, five-axis machining delivers a new dimension of flexibility and precision to material shaping.
Unlike traditional three-axis machining, which operates along the X, Y, and Z linear axes, five-axis machining introduces an additional dimension of control. This innovation is made possible by integrating a rotary table, enabling the cutting tool to move with unparalleled freedom. With the fourth and fifth axes in play, the cutting tool gains the capacity to tilt and rotate, expanding its realm of motion.
This intricate dance of multiple axes significantly enhances precision and flexibility, setting the stage for creating intricate, three-dimensional shapes and contours with unprecedented efficiency and accuracy.
Particularly useful in industries that require intricate and highly detailed components, five-axis machining produces precise, long-lasting parts for key sectors such as aerospace, automotive, and medical device manufacturing.
How does five-axis machining work?
Five-axis machining is a dynamic precision metal manufacturing process that brings a new dimension of flexibility and precision to material shaping. This innovative technique allows a cutting tool, often shorter cutting tools, to traverse along five distinct axes concurrently, significantly enhancing its capabilities. With the addition of two rotational axes (A and B) to the traditional three linear axes (X, Y, and Z), the cutting tool is no longer bound to a fixed set of movements.
These 5 axes are designated as X, Y, Z, A, and B:
X-Axis:
The X-axis is responsible for horizontal movement, enabling the cutting tool to traverse from left to right.
Y-Axis:
Representing horizontal movement from front to back, the Y-axis plays a crucial role in shaping the material.
Z-Axis:
The Z-axis oversees vertical movement, facilitating the tool’s upward and downward motions.
A-Axis:
Also known as the rotary or tilt axis, the A-axis empowers the cutting tool to pivot around the X-axis. This rotational movement allows the tool to approach the workpiece from various angles, enhancing its maneuverability and precision.
B-Axis:
Similar to the A-axis, the B-axis functions as a rotational or tilt axis but revolves around the Y-axis. It complements the A-axis, further expanding the tool’s versatility in positioning.
Combining these five axes allows for intricate and exact material shaping, making this horizontal machining method invaluable in precision metal manufacturing. Using this technology, manufacturers can easily handle complex geometries, producing components rapidly, accurately, and with a level of detail that was previously impossible with traditional machining methods.
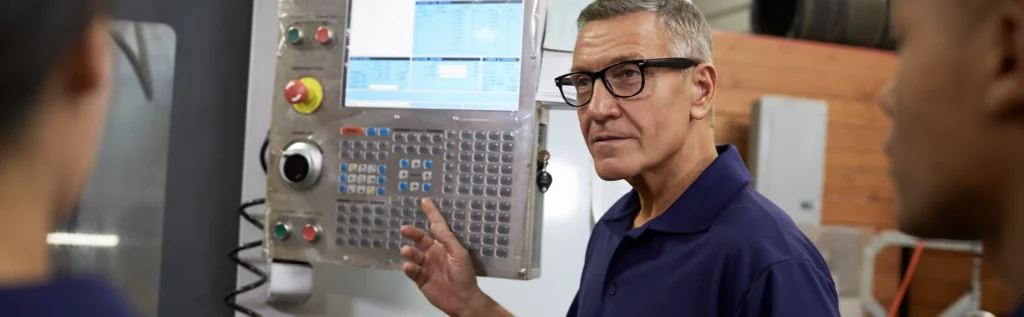
The five-axis machining process
The five-axis machining process is a sophisticated method that enables the creation of intricate parts and components quickly and easily. Here’s how it works:
- Workpiece Setup: The process commences with the workpiece, typically composed of metal, plastic, or other materials, securely affixed to the machining table. This fixation ensures stability and accuracy throughout the machining operation.
- Tool Selection: Choosing the right cutting tool is paramount and is determined by the specific requirements of the machining operation and the properties of the material being worked on.
- Toolpath Programming: A CNC (Computer Numerical Control) program outlines the cutting tool’s path. The program accounts for the intricate movements of the five axes. The program specifies the tool’s position, orientation, and speed at each juncture of the machining process, ensuring that it follows the desired trajectory.
- Machining Operation: The CNC programming is ported to the machining center, where the CNC machine’s controller interprets the instructions and translates them into actions. The controller commands the motors to orchestrate the synchronized movements of all five axes, enabling the cutting tool to access a multitude of angles and positions. This versatility allows for the creation of intricate cuts and the precise shaping of the workpiece.
- Constant Monitoring: A vigilant machine operator or a computerized system monitors the process continuously throughout the machining process. Monitoring involves assessing and adjusting factors such as tool wear, cutting speed, and coolant flow. These interventions are crucial in maintaining the quality and accuracy of the finished part.
- Completion: The finished part is carefully removed after the CNC machine has completed its machining operation. Additional post-processing steps may be required based on the specific requirements. Deburring or surface finishing may be required to ensure the final part meets the desired quality and appearance specifications.
What are the benefits of multi-axis machines in sheet metal machining?
Multi-axis machining centers, like the ones on the Pinnacle Precision production floor, are essential in fabricating precision sheet metal parts because they offer our Production team greater accuracy, flexibility, and efficiency.
We utilize multi-axis machines to produce sheet metal parts with complex designs found in components our customers in the medical, aerospace, and energy industries use.
These machines perform drilling, milling, tapping, and threading operations efficiently because there’s only one setup.
Pinnacle Precision utilizes multi-axis machines to maximize speed, accuracy, efficiency, and savings whenever possible.
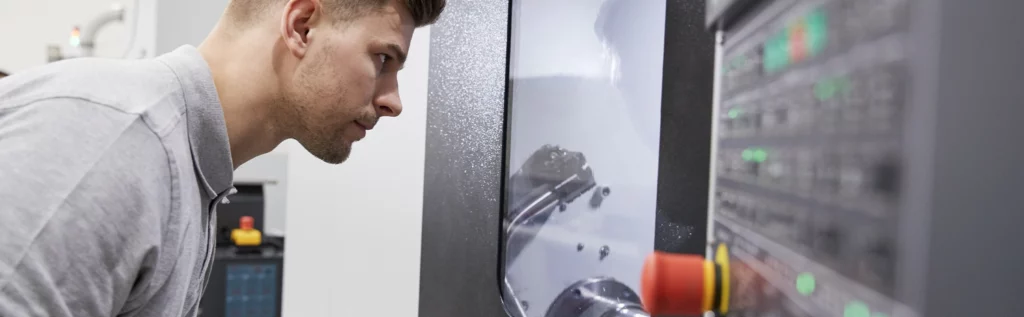
The Pinnacle Precision Difference
The Pinnacle difference lies in our power of production. Our 73,000-square-foot facility has an expansive production floor that boasts nine machining centers, enabling us to deliver accurate parts in a fast-paced environment. Partnered with our Technical and Production crew, these machines allow us to form a variety of sheet metal grades to the tightest tolerances.
Our cutting-edge technology includes:
- (1) 5-axis machining center
- (4) CNC vertical machining centers
- (1) CNC turning center
Each project that comes into Pinnacle’s Southern California headquarters receives the highest level of attention. Our Customer Support team excels in translating customer needs into actionable plans for our Technical, Production, and Quality Assurance teams.
Our CNC machine manufacturing experts utilize CNC laser cutting and punch presses for precise sheets delivered to our machining, forming, welding, and finishing departments. From there, we help our customers with assembly, hardware installation, and seal applications before Pinnacle’s quality assurance team carefully looks at the final product.
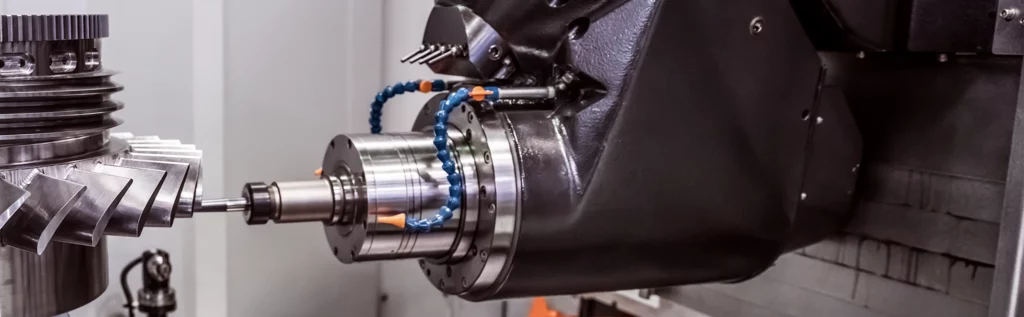
How Five-Axis Machining Leads to Better Total Assembly Products
5-axis machining enables manufacturers to achieve unparalleled precision in crafting intricate components, ultimately creating superior total assembly products.
At Pinnacle, we leverage our advanced 5-axis machining centers to produce more reliable, durable assemblies that resist corrosion and environmental factors. This level of precision delivered by 5-axis machining leads to better total assembly products and happier customers.
The Future of Five-Axis Machining
Five-axis machining is a cutting-edge technique that allows manufacturers to craft complex, highly detailed components with precision and efficiency. Empowering manufacturers to produce parts that were once challenging or impossible stands as a testament to the continuous advancement in precision metal manufacturing.
If you’re looking for a trusted partner in five-axis machining, you can’t go past the team at Pinnacle. Our CNC-powered multi-axis mills produce sheet metal parts and metal components to the tightest tolerances used by medical, aerospace, defense, communications, technology & information, entertainment, and renewable energy companies.