Sheet metal fabrication is the cornerstone of modern manufacturing, responsible for durable, customizable components used in industries ranging from aerospace to electronics.
By manipulating flat metal sheets into complex shapes, this powerful process enables manufacturers to deliver precise, reliable parts tailored to meet the unique demands of various applications.
With over 50 years of experience, Pinnacle Precision delivers a new level of precision. Experts in all aspects of sheet metal fabrication, our focus on care, craftsmanship, and accuracy allows us to supply world-class parts and assemblies to support our customers. Our 73,000-square-foot manufacturing floor, powered by cutting-edge 5-axis CNC machining technology, allows us to streamline prototype and production runs with unmatched precision and cost-efficiency.
In this article, we’ll explore the fundamentals of sheet metal fabrication, including core techniques, material options, and key industry applications, while highlighting how Pinnacle Precision leads the way in delivering high-quality, customized solutions.
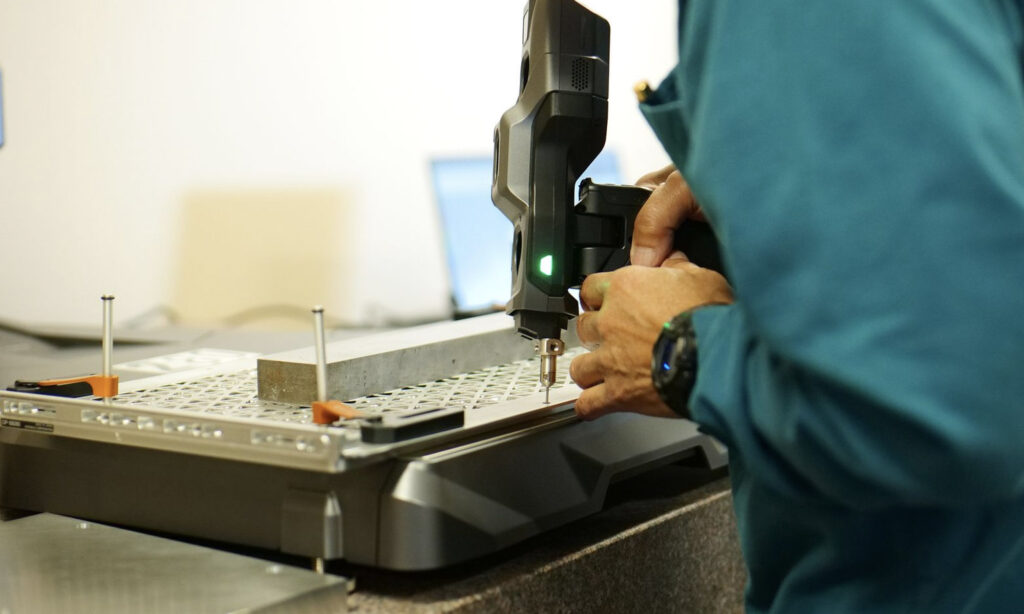
What is Sheet Metal Forming, and How Does it Work?
Sheet metal forming is a fabrication process that transforms flat metal sheets into complex shapes and structures by applying force. This versatile method is widely used across industries to create components with precise dimensions and specifications, leveraging techniques such as bending, drawing, and punching.
Stages of Sheet Metal Forming
- Design Phase:
Every project begins with detailed designs and specifications to ensure the final product meets exact requirements. Advanced CAD software is often used to model components and simulate their performance. - Cutting and Cleaning:
The metal sheet is cut to the required dimensions using techniques like laser cutting or shearing. The material is then cleaned to remove impurities and ensure smooth forming. - Forming and Finishing:
The cleaned sheet is shaped into the desired geometry using forming techniques. Once formed, components undergo finishing processes like grinding, deburring, and surface treatments to enhance durability and aesthetics.
Here at Pinnacle Precision, each project that comes into our Southern California headquarters receives the highest level of attention. Our Customer Support team excels in translating customer needs into actionable plans for our Technical, Production, and Quality Assurance teams. Our crews work with product sizes ranging from inches to yards, a broad range of sheet metal alloys and finishes, and run from prototype to production.
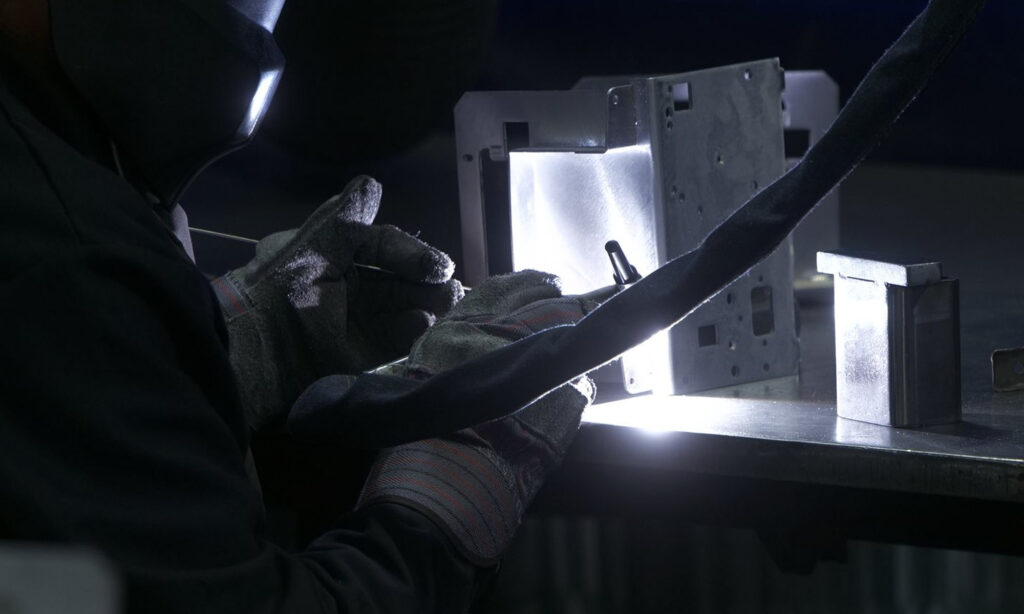
Core Techniques in Sheet Metal Fabrication
Sheet metal fabrication involves a variety of techniques designed to manipulate metal into the desired shape or structure. Each method has specific applications and benefits, depending on the complexity and functionality of the final product.
Cutting
Cutting is one of the most fundamental processes in sheet metal fabrication, dividing raw sheet metal into manageable sizes or shapes.
- Laser Cutting: Offers high precision and clean edges, ideal for intricate designs.
- Plasma Cutting: Suitable for thicker materials but less precise than laser cutting.
- Shearing: A cost-effective method for straight cuts but less versatile for complex designs.
Forming
Forming involves shaping metal through bending, stamping, or punching.
- Bending: Uses press brakes to create angular bends when bending sheet metal.
- Stamping: Ideal for high-volume production of detailed designs.
- Punching: Creates holes or cutouts in metal sheets with precision.
Welding and Joining
Welding and joining processes combine metal components into durable assemblies.
- MIG Welding: Efficient and versatile for thicker materials.
- TIG Welding: Offers superior precision and control for delicate parts.
- Spot Welding: Ideal for joining thin sheets on your sheet metal workpiece.
At Pinnacle Precision, we employ advanced CNC technology and state-of-the-art equipment to ensure each process meets the highest quality standards.
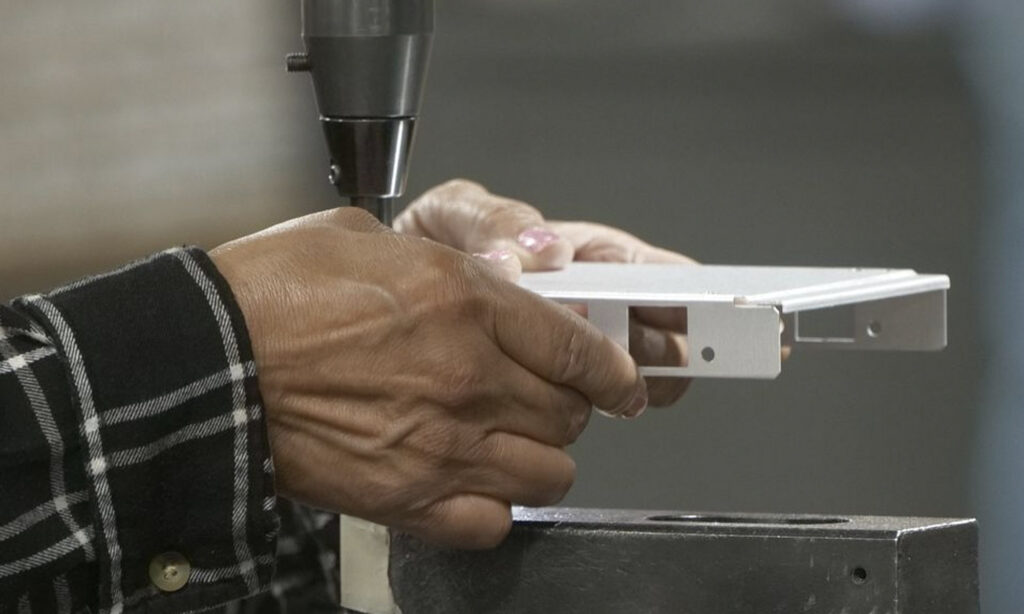
Commonly Used Materials in Sheet Metal Fabrication
The right material is critical in sheet metal fabrication, as your choice can directly impact the durability, weight, and performance of the final product.
The choice of material also depends on the types of sheet metal available, such as stainless steel, aluminum, copper, or brass, each offering unique properties suited to specific applications. The material thickness also plays a crucial role in determining the strength and flexibility of the final component, with thinner sheets ideal for intricate designs and thicker sheets providing greater structural integrity.
Understanding the sheet form — whether it’s flat, coiled, or pre-cut — ensures compatibility with the intended fabrication processes and contributes to achieving optimal performance and precision in the finished product.
Stainless Steel
Stainless steel is a common material in sheet metal fabrication due to its exceptional corrosion resistance, durability, and strength, making it ideal for demanding applications. Whether using cold-rolled steel for its smooth finish and precise dimensions or hot-rolled steel for its cost-efficiency and malleability, stainless steel offers versatility that caters to both aesthetic and functional requirements in various industries.
- Strengths: High corrosion resistance, durability, and aesthetic appeal.
- Applications: Medical devices, food processing equipment, and architectural components.
Aluminum
Aluminum is a popular choice in sheet metal fabrication due to its lightweight nature, excellent corrosion resistance, and ease of machinability. Its high strength-to-weight ratio makes it ideal for applications in aerospace, automotive, and electronics, where reducing weight without compromising durability is critical. Additionally, aluminum’s malleability allows for the creation of complex shapes and designs, making it a versatile material for custom manufacturing.
- Strengths: Lightweight, corrosion-resistant, and easy to machine.
- Applications: Aerospace, automotive, and electronics.
Copper
Copper is frequently used in sheet metal fabrication because of its superior thermal and electrical conductivity, making it essential for electrical components, heat exchangers, and roofing materials. Its natural resistance to corrosion and ability to form complex shapes further enhance its suitability for both functional and decorative applications.
- Strengths: Excellent electrical and thermal conductivity.
- Applications: Electrical components, heat exchangers, and roofing materials.
Brass
Brass is commonly used in sheet metal fabrication due to its excellent malleability, corrosion resistance, and unique aesthetic appeal. Its ability to be easily shaped into intricate designs makes it ideal for decorative and functional applications, such as architectural elements, musical instruments, and plumbing fixtures. Brass’s natural antimicrobial properties also make it a preferred material for applications in healthcare and food processing industries.
- Strengths: Corrosion resistance, malleability, and a unique appearance.
- Applications: Decorative hardware, musical instruments, and plumbing fixtures.
Each material brings specific advantages to sheet metal fabrication, and Pinnacle Precision provides expert guidance in selecting the best option for your application.
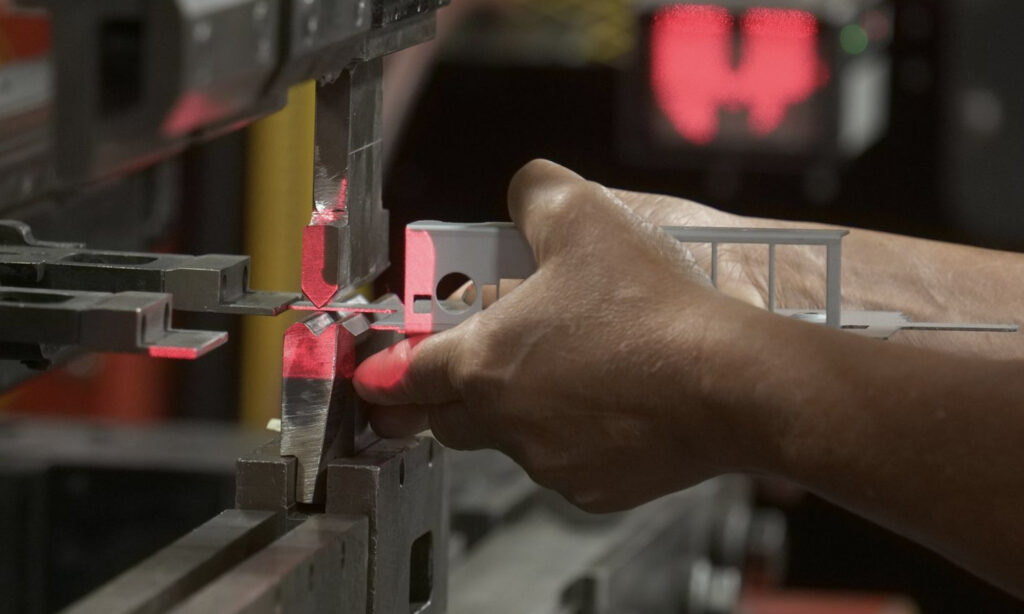
The Main Benefits of Sheet Metal Forming
Sheet metal forming offers unparalleled advantages in creating high-quality, customized components. Its flexibility and efficiency make it a preferred choice across industries ranging from automotive to aerospace.
Here are the main benefits of this versatile fabrication process:
-
Versatility in Design
Sheet metal forming allows for the creation of components in almost any shape, making it essential for custom manufacturing projects that require precise dimensions and complex contours. Whether it’s a simple bracket or an intricate enclosure, sheet metal can be manipulated to meet specific design needs, offering endless possibilities for engineers and manufacturers.
-
High Efficiency
The processes involved in sheet metal forming are highly efficient, enabling quick production of large quantities. This makes it ideal for high-volume manufacturing, where speed and consistency are critical. Industries such as electronics and construction rely on sheet metal forming to meet tight deadlines while maintaining quality.
-
Cost-Effectiveness
Compared to other forming methods, sheet metal forming is a cost-effective solution. Not only does it streamline production, but the durability of metal components ensures a longer product life cycle, reducing the need for frequent replacements. This makes it a smart investment for manufacturers focused on long-term value.
-
Strength and Durability
Sheet metal components are robust and capable of withstanding extreme conditions, making them indispensable in applications like automotive and aerospace. Whether it’s exposure to high temperatures or heavy mechanical stress, products made from sheet metal offer unmatched durability and reliability.
-
Reduced Waste
Modern sheet metal forming techniques, such as CNC machining and advanced cutting methods, maximize material usage and minimize waste. This not only supports sustainable manufacturing practices but also helps manufacturers optimize costs while reducing environmental impact.
-
Improved Precision
Technological advancements, including CNC machining and laser cutting, have significantly enhanced the precision of sheet metal forming. These innovations ensure that components meet strict tolerance thresholds, which is crucial for applications where accuracy is paramount, such as medical devices and electronics.
The versatility, efficiency, and sustainability of sheet metal forming make it a vital process in today’s manufacturing landscape. By leveraging its many benefits, businesses can produce high-quality components tailored to their needs while maintaining cost-effectiveness and precision.
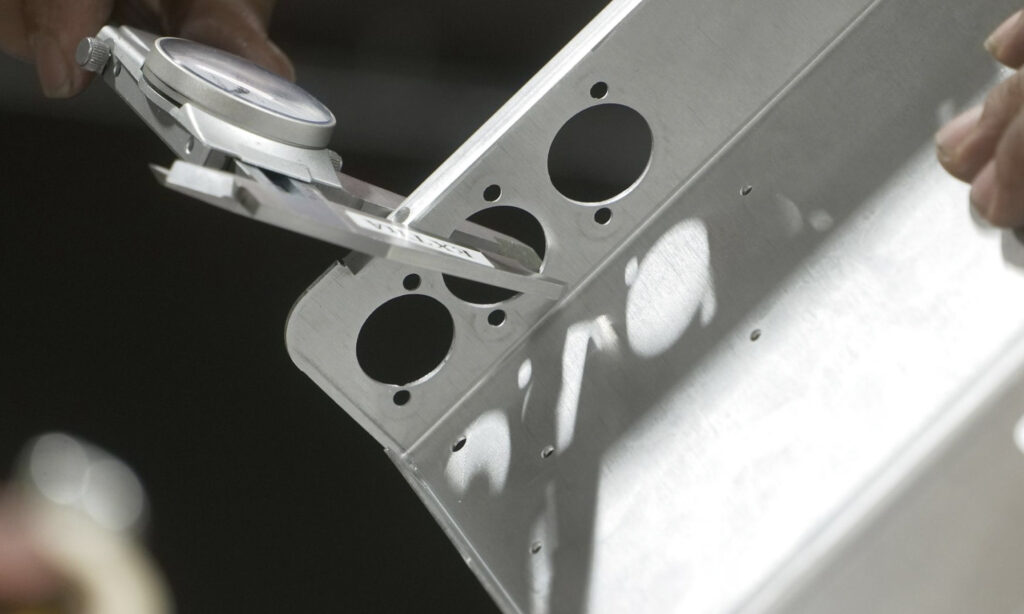
Applications of Sheet Metal Fabrication Across Industries
With its unique ability to produce components that combine functionality, strength, and precision, sheet metal fabrication has become the preferred process for a wide range of critical industries.
Medical Devices
Precision-fabricated components ensure the reliability and safety of surgical instruments, diagnostic equipment, and implantable devices.
Aerospace
Fabricated sheet metal components are essential for creating lightweight, durable parts used in aircraft and spacecraft, such as structural panels and heat exchangers.
Electronics
Sheet metal fabrication provides enclosures, brackets, and heat sinks for electronic devices, ensuring protection, durability, and effective thermal management.
Construction
Custom metal components, such as beams, brackets, and roofing elements, contribute to the architectural and structural integrity of buildings and infrastructure.
Here at Pinnacle Precision, we deliver mission-critical parts, components, and assemblies to manufacturers in a wide range of industries.
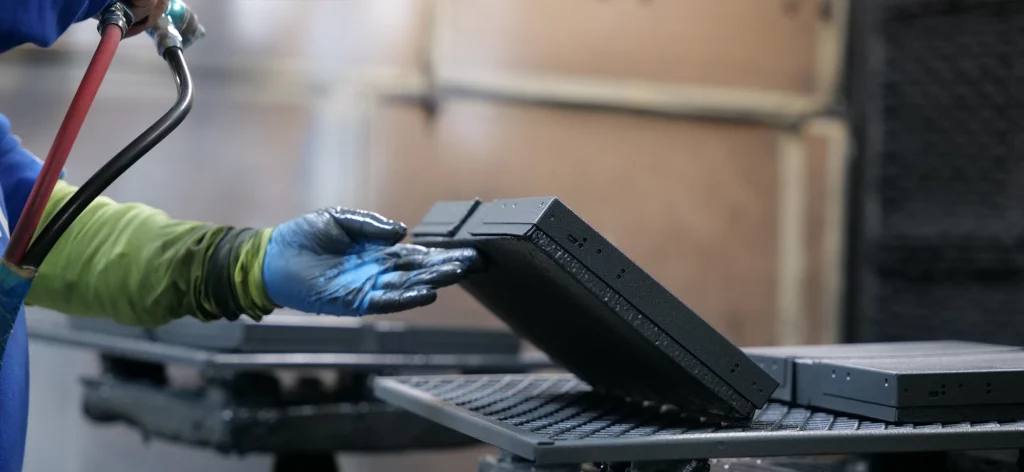
Experts in Precision Sheet Metal Fabrication
At Pinnacle Precision, we combine decades of experience with advanced technology to deliver industry-leading sheet metal fabrication solutions.
Our Capabilities
- Cutting, Punching, Forming, Welding, and Grinding: From intricate cuts to robust welds, we provide a full suite of fabrication services.
- Advanced CNC Technology: Our production floor features CNC-powered laser cutting and punching machines, dozens of press brakes with 50- to 125-ton capabilities, and dedicated spaces for welding and grinding.
Our Proven Sheet Metal Forming Process
Our technical, production, and quality assurance teams work collaboratively to ensure every part meets our exacting standards. Our integrated approach combines expertise, state-of-the-art equipment, and a commitment to excellence.
By expertly forming sheet metal, we proudly support industry leaders in medical, aerospace, defense, communications, technology, entertainment, and renewable energy. By leveraging our advanced capabilities, we help clients achieve superior outcomes in their most critical projects.
Our Proven Sheet Metal Forming Process
Our technical, production, and quality assurance teams work collaboratively to ensure every part meets our exacting standards. Our integrated approach combines expertise, state-of-the-art equipment, and a commitment to excellence.
By expertly forming sheet metal, we proudly support industry leaders in medical, aerospace, defense, communications, technology, entertainment, and renewable energy. By leveraging our advanced capabilities, we help clients achieve superior outcomes in their most critical projects.
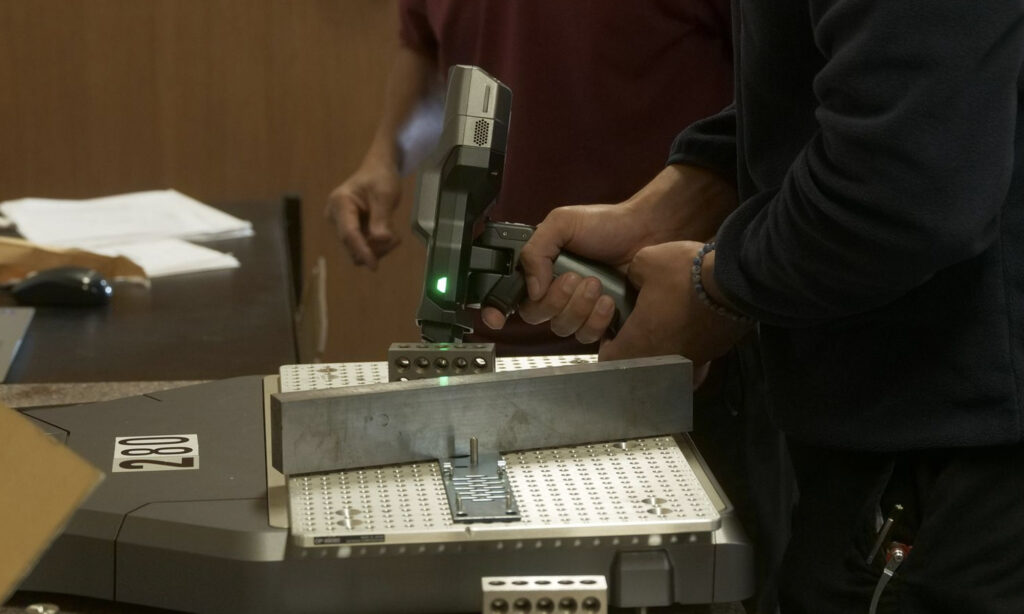
Power Up Your Product Design and Manufacturing
Understanding the fundamentals of sheet metal fabrication — techniques, materials, and applications — empowers businesses to make informed decisions in product design and manufacturing. And now, with the knowledge provided in this article, you can too.
At Pinnacle Precision, we have over 50 years of experience working with industry-leading companies that shape our future in medical, communications & technology, renewable energy, aerospace, and defense fields.
Working with a range of sheet metals, we consistently deliver high-quality, customized components designed to meet the unique demands of industries worldwide. Our advanced processes ensure parts can withstand harsh environments while maintaining their performance and aesthetic appeal.
Ready to elevate your manufacturing capabilities?
Talk with the team at Pinnacle Precision today to learn more about how our expertise and solutions can drive the success of your next sheet metal fabrication project. Together, we’ll bring your vision to life with precision and reliability.