Precision sheet metal forming is paramount in today’s leading industries. At Pinnacle Precision, we specialize in transforming raw metal sheets into sophisticated components that fuel innovation for our customers in the defense, medical, communications, aerospace, and renewable energy industries.
Precision sheet metal forming has become crucial for today’s leading industries to deliver accurate, reliable, and durable parts.
Essential for creating complex shapes and structures from flat metal sheets, sheet metal forming processes play a pivotal role in modern manufacturing, producing intricate and lightweight components with high precision and consistency for a wide range of industries.
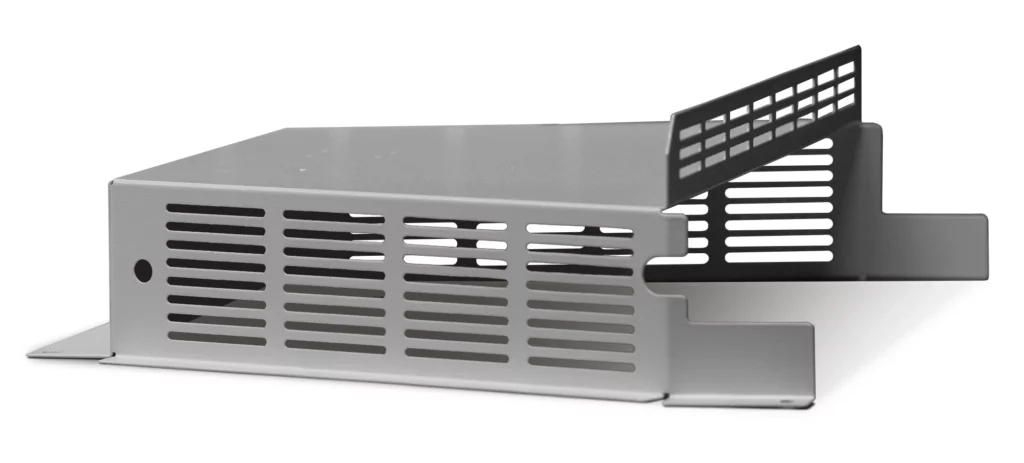
In addition to creating aesthetically pleasing designs with complex geometries, the process ensures optimal functionality and structural integrity. From intricate brackets to seamless body panels, sheet metal forming significance lies in its capacity to transform a raw metal sheet into sophisticated components that drive innovation and advancement across various manufacturing sectors.
In the world of precision metal manufacturing, accuracy is everything. Precise sheet metal forming is paramount because even the smallest deviation or discrepancy in the forming process profoundly impacts the final product’s quality, performance, and fit.
Experts in sheet metal forming operations, Pinnacle has quickly become the proven partner for precision bending and forming sheet metal. And it’s easy to see why.
Pinnacle Precision manufactures parts used across the world’s most advanced and vital industries, including medical, aerospace, information & communications, energy, and entertainment. Our progressive approach to every capability means that parts created here can withstand the harshest environments and look good year after year.
TECHNIQUES IN THE SHEET METAL FORMING PROCESS
Let’s start with the basics. The term sheet metal refers to thin, flat metal pieces formed through industrial processes. Sheet metal is one of the most versatile materials available to manufacturers and fabricators, with applications as varied as life-saving medical machines, enclosures for computers, or airplane cabin infrastructure.
Sheet metal forming involves various processes that subject the metal sheet to controlled forces, either through mechanical or hydraulic means, to deform it into the desired shape – modifying rather than removing.
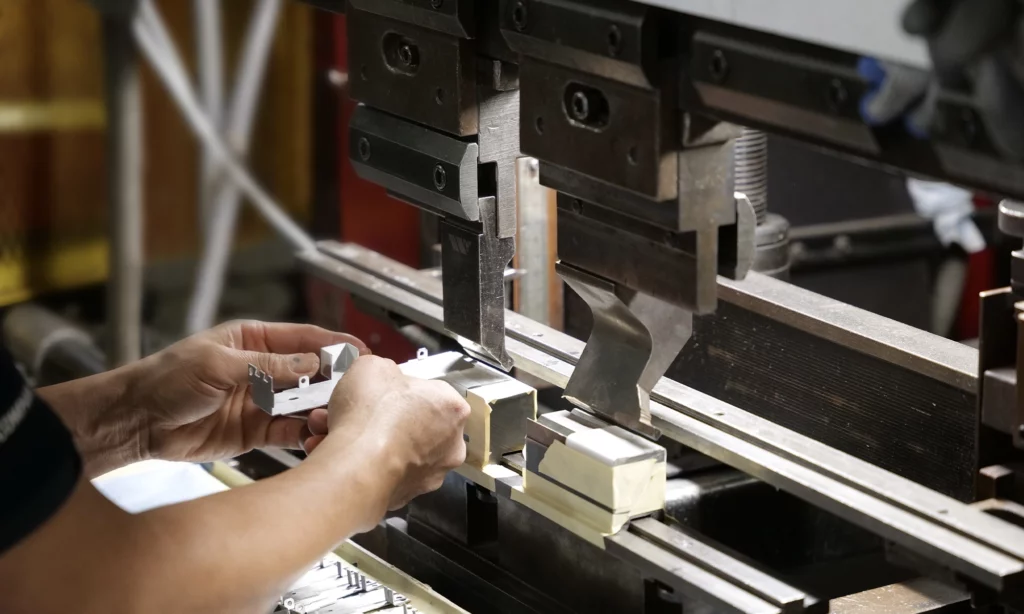
There are many types of sheet metal forming, from free forming to stretch forming, press forming, and cold forming. Its ability to consistently produce precise components plays a pivotal role in modern manufacturing for industries ranging from automotive to aerospace.
Sheet metal forming encompasses various techniques tailored to specific design requirements and production scales. One of the most common methods is “bending,” which involves deforming the metal along a straight axis to achieve angles and contours. “Deep drawing” creates intricate three-dimensional shapes, pulling the metal into a die cavity under high pressure. “Stamping” employs custom dies to cut and shape metal sheets precisely, while “rolling” produces continuous profiles through gradual shaping between rollers.
Our experience at Pinnacle Precision is delivering flat, bent, stamped, curved, and flange parts via CNC cutting, punching, and forming processes. Our Technical team sets up exacting CNC specifications that enable infinite back gauge and ram settings, ensuring accurate metal parts with limited material waste.
Our expert Production crew has mastered the sheet metal forming process. The team utilizes specialized forming tools, including 14 press brakes, while forming precision sheet metal parts for our customers.
Our collection of brakes and tools ensures we deliver the parts needed on time with the highest accuracy possible. Partnered with Pinnacle’s Technical and Production crew, these machines allow us to form a variety of sheet metal grades to the tightest tolerances.
For more complex geometries, “hydroforming” utilizes fluid pressure to mold metal against a die, while “embossing” imparts textures or patterns onto the sheet surface. The “punch and die” method is commonly used to accurately create intricate shapes, guiding the metal sheet through a series of controlled movements.
The process seamlessly combines the finesse of craftsmanship with the precision of machinery, enabling the transformation of a flat sheet into a multi-dimensional component along a carefully curated straight line.
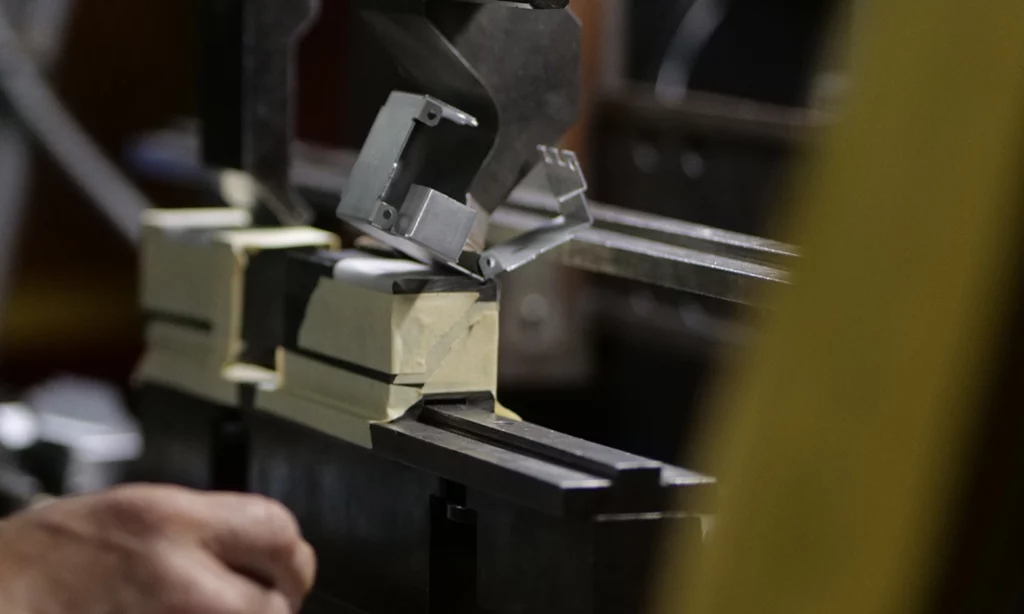
MATERIAL CHOICES & THEIR SIGNIFICANCE
A variety of different metals can be processed into sheet metal, including:
- Aluminum
- Steel
- Brass
- Tin
- Copper
- Nickel
- Titanium
- Plus gold, silver, and platinum – for decorative purposes.
Selecting suitable materials for sheet metal forming processes is paramount in achieving optimal performance and durability. Cold-rolled steel, prized for its enhanced strength and smooth finish, is a staple in industries requiring robust components, such as automotive chassis and structural elements.
Aluminum finds its niche in aerospace and consumer electronics due to its low density and excellent corrosion resistance. At the same time, stainless steel shines in applications like kitchen appliances and medical equipment because of its high-temperature corrosion resistance and reliability.
What we use at Pinnacle:
General material tolerances
-
Cold Rolled Steel – 24 gauge to 3/16”
-
Aluminum – .020 to .187
-
Stainless Steel – 24 gauge to 11 gauge
Each material’s distinct properties directly influence its applications, so you must consider factors such as performance, environmental exposure, and design constraints when choosing the right material for your product.
VERSATILITY & APPLICATIONS OF SHEET METAL
A versatile, consistent, high-quality process, sheet metal forming creates accurate metal parts with limited material waste for various industries. The malleability of sheet metal allows for creating complex shapes, while its durability guarantees performance in high-stress environments.
Its versatility is showcased in producing intricate components for medical devices, where precision is paramount for patient well-being. The aerospace sector relies on sheet metal forming to craft lightweight yet resilient components that can withstand extreme conditions. This technique is indispensable in automotive design, architecture, electronics, and beyond.
Our Production team uses CNC cutting, punching, and forming processes to produce flat, bent, stamped, curved, and flange parts.
Parts fabricated during this process include plates, brackets, enclosures, frames, cabinets, carts, vents, hinges, and connectors for customers from leading medical, aerospace, information and communications technology, energy, and entertainment companies.
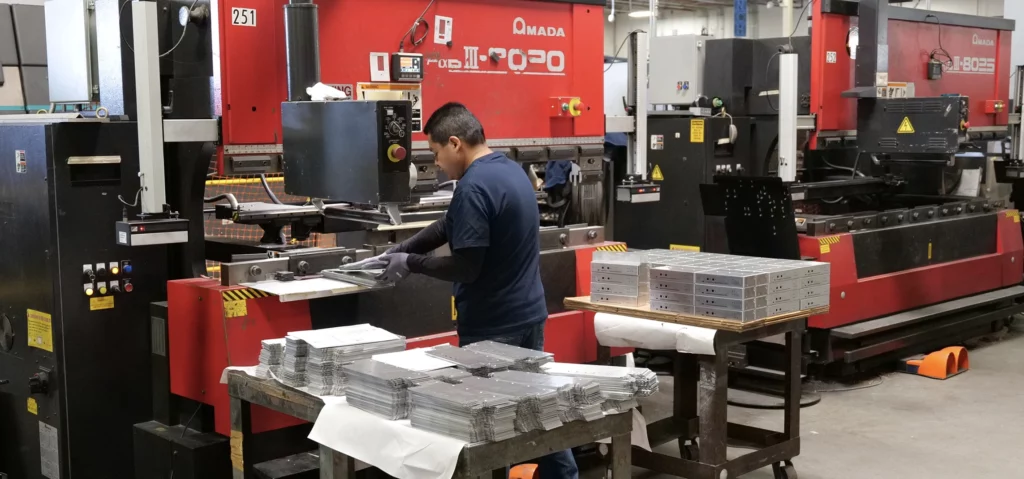
Ensuring Quality in Sheet Metal Forming
In the competitive landscape of modern manufacturing, the quality of sheet metal forming underpins product reliability and customer satisfaction.
Every facet of the process, from material selection to tooling design and production, must adhere to strict standards and specifications to ensure quality. Minor variations in dimensions or material properties can propagate throughout the production chain, leading to compromised fit, functionality, and structural integrity of the final product. Quality control protocols, rigorous inspection techniques, and advanced measurement technologies are essential to identify even the slightest deviations and rectify them promptly.
Pinnacle has a company-wide commitment to quality. Our quality assurance team carefully looks at every stage of the process to ensure only the best final product is delivered.
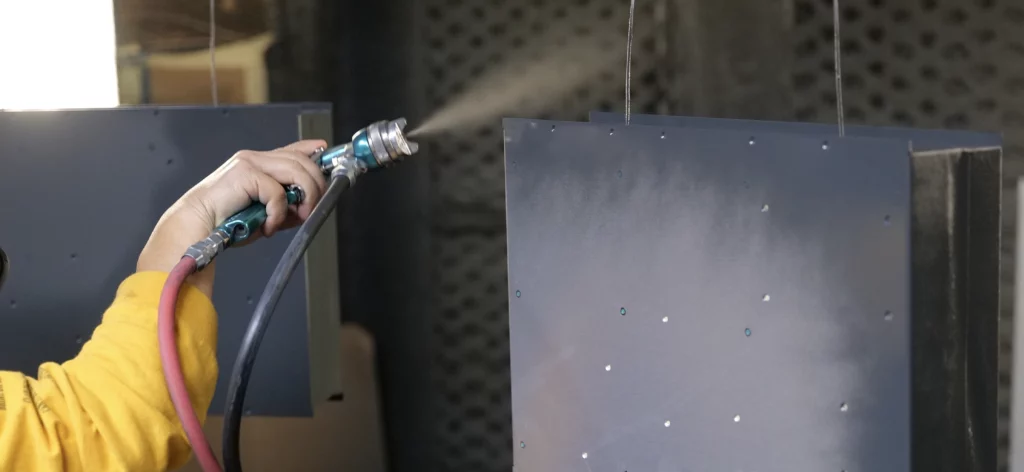
The Pinnacle Process: From Consultation to Completion
The difference between Pinnacle and any other company is our team-forward integrated approach and solutions-first mentality.
Each project in Pinnacle’s Southern California headquarters receives the highest attention. Our Customer Support team excels in translating customer needs into actionable plans for our Technical, Production, and Quality Assurance teams.
Our manufacturing experts utilize CNC laser cutting and punch presses for precise sheets delivered to our machining, forming, welding, and finishing departments. From there, we help our customers with assembly, hardware installation, and seal applications before Pinnacle’s quality assurance team carefully looks at the final product.
Industries That Benefit From Sheet Metal Forming
Sheet metal forming is revolutionizing how we live, work, and explore. Parts created by sheet metal forming are everywhere in our daily lives, from drink cans to protective housings.
Several pivotal industries greatly benefit from sheet metal forming, especially those that demand exacting standards and innovative solutions that can perform in demanding environments. In the medical field, intricate and reliable sheet metal components are essential for manufacturing advanced imaging devices, surgical instruments, and implantable medical devices. The aerospace industry relies heavily on sheet metal forming to craft lightweight yet resilient structural elements, engine components, and aerodynamic surfaces that ensure safe and efficient air travel.
Precision sheet metal parts are also used in the information and communications sector to manufacture high-performance server racks, networking equipment, and electronic enclosures.
DISCOVER THE PINNACLE DIFFERENCE
When it comes to precision metal forming, there’s simply no one better in the business. Our teams boast decades of experience, working with product sizes ranging from inches to yards and a broad range of sheet metal alloys and finishes.
Customers from leading defense, medical, aerospace, information and communications technology, energy, and entertainment companies come to Pinnacle Precision because they’ve experienced a new level of precision.
The difference between Pinnacle and any other company is our team-forward integrated approach and solutions-first mentality. We look forward to proving our promise to you