Different metal finishing techniques have unique advantages and applications, with painting being versatile and visually appealing, powder coating providing exceptional durability and eco-friendliness, and silk screening allowing for intricate and detailed designs.
As the final step in the manufacturing process, metal finishing plays a vital role in enhancing various metal products’ appearance, durability, and functionality. From industrial applications to decorative purposes, the right metal finishing technique can transform raw manufactured parts into ready-to-use components with the necessary protection against corrosion and wear.
Experts in finishing metal parts, Pinnacle Precision’s Finishing department is one of Southern California’s best sheet metal finishing companies. For Pinnacle’s commercial paint, powder coating, and silkscreening crews, making metal surfaces pretty and protected is priority number one. The surface finishing team uses industry-leading materials to enhance the strength, durability, and appearance of every painted metal part produced here, including paint and powder specially designed for use in medical, aerospace and defense, and harsh environments.
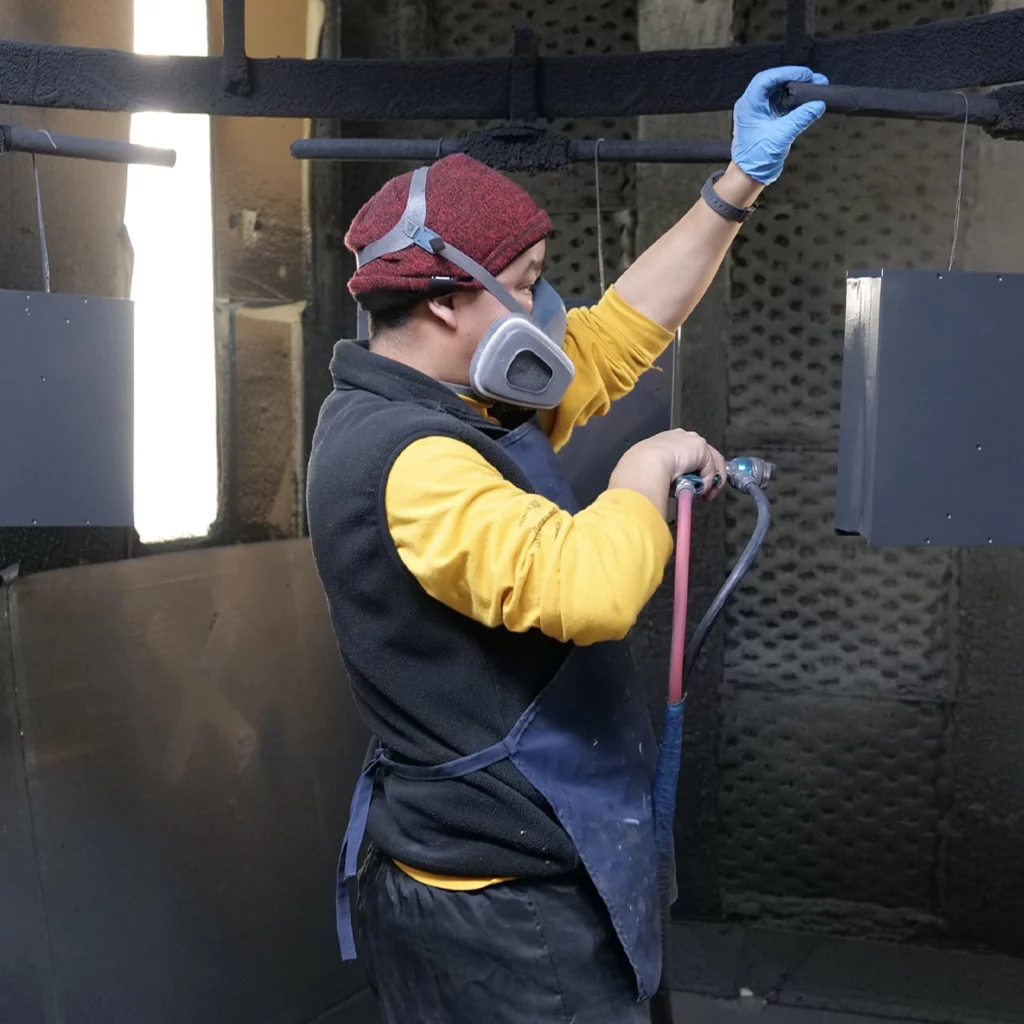
With various surface finishing techniques available, choosing the metal finishing process best suited to you can be difficult. In this comprehensive guide, we review three popular metal finishing techniques: painting, powder coating, and silk screening, looking at specific applications and key considerations for choosing both a metal finishing process and metal finishing partner.
Importance of Metal Finishing and Metal Finishing Processes
The importance of metal finishing cannot be overstated. Whether for aesthetic appeal, functional enhancement, or value add, metal finishes provide numerous benefits to a wide range of metal products.
The main advantages of metal finishing include:
- Increased durability
- Improved decorative appeal
- Enhanced electrical conductivity
- Higher electrical resistance
- Higher chemical resistance
- Higher tarnish resistance
Let’s take a closer look at the importance of metal finishing processes.
Functional Enhancement:
Metal finishing techniques are specifically designed to improve the functional properties of metal surfaces. For example, through a metal finishing process like polishing and grinding, finishes can reduce surface friction between metal components, allowing for smoother movement and increased efficiency. Additionally, certain finishes can enhance electrical conductivity, making them ideal for applications requiring optimal electrical performance.
With several different types of metal finishing available, one of their most significant advantages is the ability to create corrosion resistance for the metal’s surface. By applying protective coatings or surface treatments, finishes create a barrier that shields metal from environmental factors such as moisture, chemicals, and abrasion. This protection helps prevent rust, degradation, and premature failure, ultimately extending the lifespan of the metal product.
Aesthetic Enhancement:
Metal finishing techniques play a pivotal role in enhancing the visual appeal of metal products. Whether you’re looking for a sleek and reflective metal surface with slightly rounded edges or a matte finish with a textured pattern, metal finishing offers endless possibilities.
Surface finishing removes surface roughness and sharp edges and eliminates flaws such as scratches, blemishes, and any surface defects, resulting in a smooth and flawless appearance.
Value Add:
Metal finishing adds significant value throughout the product lifecycle by improving the resistance to corrosion, wear, and environmental factors, which increase the lifespan of metal products. This benefits the end customer by providing a durable and long-lasting product and reduces the need for frequent maintenance or replacement, resulting in cost savings.
The aesthetic appeal achieved through metal finishing can profoundly impact a product’s perceived value. This enhanced perceived value can justify premium pricing, differentiate products in the market, and ultimately increase sales.
- Did you know that metal ions serve as the building blocks for various common metal surface finishes, enabling the creation of functional and visually appealing metal surfaces for a diverse range of applications?
Choosing the Right Surface Finishing Technique
With a wide variety of metal surface finishes available, how do you choose the right one?
To ensure you get the right outcome for a particular application, several factors must be carefully considered before deciding. First and foremost, the type of metal used plays a vital role. Different metals have unique characteristics and reactivity, making some more suitable for certain finishing processes than others.
Additionally, understanding the part’s function is essential; techniques like powder coating or electroplating might be preferred for functional parts subjected to wear, corrosion, or electrical conductivity requirements.
Environmental considerations also come into play, with eco-friendly options such as powder coating gaining popularity. Cost-effectiveness is another critical factor; some techniques may have higher initial costs but offer better long-term value through increased durability and reduced maintenance needs. Desired aesthetics should align with the finishing technique’s capabilities, be it painting for various colors or anodizing for vibrant and durable finishes.
Ultimately, the right metal finishing technique will best meet your project’s specific functional, aesthetic, and economic requirements.
Painting as a Metal Finishing Technique
Painting is one of the most versatile and widely used metal finishing techniques. As a metal finishing technique, painting offers a versatile and visually appealing way to protect and enhance metal surfaces.
The process of painting metal involves several key steps to ensure a durable and professional-quality finish.
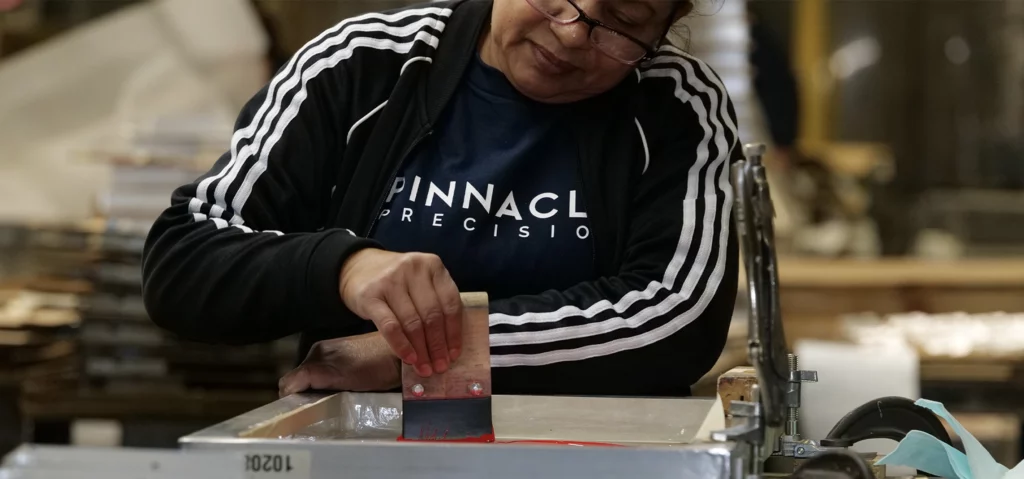
The key steps include:
Surface Preparation: The first step in painting metal is proper surface preparation. It involves thorough surface cleaning to remove dirt, grease, rust, or contaminants that may affect paint adhesion. This can be achieved through methods like degreasing, sanding, or using chemical cleaners. Minor surface imperfections can be filled or repaired at this stage if necessary.
Priming: Applying a primer is essential, especially when dealing with bare metal or surfaces with significant imperfections. Primers create a bonding layer between the metal and the paint, enhancing adhesion and promoting a smooth finish.
Application: The actual painting process involves carefully applying paint onto the prepared metal surface. Various techniques can be used, including brush painting, spray painting, or dipping, depending on the size and complexity of the metal object. Spray painting is often preferred for larger projects or to achieve a smooth and consistent finish.
Multiple coats of paint are typically applied to achieve an even and durable finish.
Finishing and Curing: Once all the coats have been applied, the painted metal needs to dry and cure thoroughly. Curing time may vary based on the paint type and environmental conditions. Adequate curing ensures the paint reaches its maximum hardness and durability.
Key benefits of painting as a metal finishing technique:
Corrosion Protection: Painting creates a protective barrier between the metal surface and the surrounding environment, safeguarding it from rust and corrosion. This is particularly important for metal objects exposed to moisture, chemicals, and harsh weather conditions.
Enhanced Aesthetics: Painting allows for endless possibilities in terms of color, texture, and visual effects. It provides an opportunity to customize metal surfaces, making them visually appealing and suitable for specific design requirements.
Versatility: With the ability to paint on various metal substrates, this technique is applicable to a wide range of products, from industrial components to decorative objects, enabling consistent finishes across different materials.
Easy Maintenance: Painted metal surfaces are generally easy to clean and maintain, reducing the need for frequent touch-ups and maintenance, which can lead to cost savings in the long run.
Cost-Effectiveness: A cost-effective metal finishing solution compared to other methods like electroplating or anodizing. It provides an attractive finish at a relatively lower cost.
Powder Coating as a Metal Finishing Technique
Powder coating has gained immense popularity recently due to its exceptional durability, environmental friendliness, and wide range of color options. This electrostatic process involves applying a dry powder to the metal surface, which is then cured to create a resilient and attractive finish.
The process of powder coating involves several distinct steps, ensuring a consistent and high-quality finish.
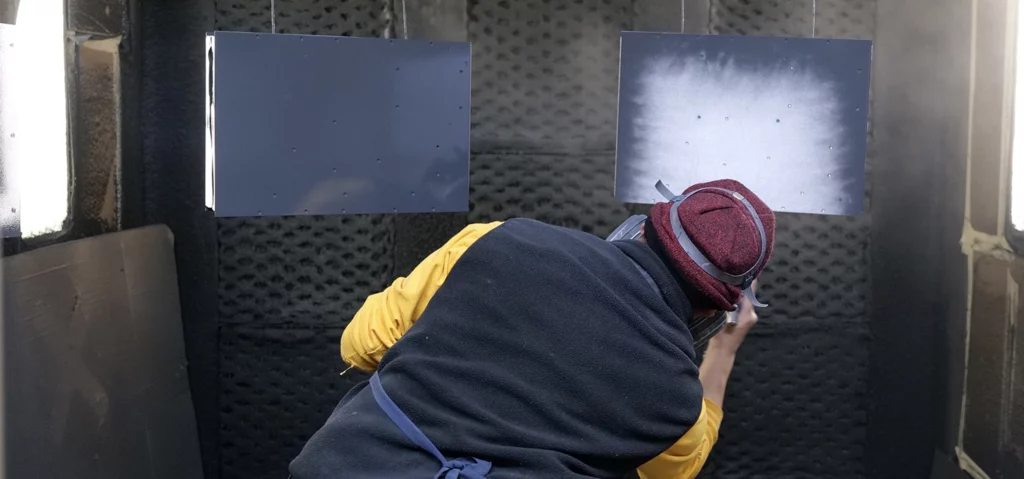
The key steps include:
Surface Preparation: The first step in powder coating is surface preparation. It involves cleaning the metal surface thoroughly to remove any dirt, grease, rust, or contaminants that may hinder adhesion. Depending on the condition of the metal, this step may include sandblasting, chemical cleaning, or mechanical cleaning methods.
Pre-Treatment: After cleaning, the metal may undergo a pre-treatment process. This step typically involves applying a conversion coating or chemical treatment to enhance adhesion, improve corrosion resistance, and create a clean surface for the powder to bond effectively.
Application: The actual powder coating application can be done using various methods, including electrostatic spray guns or fluidized bed systems. In electrostatic spray coating, the powder particles are electrostatically charged as they are sprayed onto the grounded metal substrate, resulting in an even and uniform coating.
Curing: The metal object is transferred to a curing oven once the powder has been applied. During the curing process, the powder particles melt and fuse together, forming a continuous and durable film on the metal surface. Curing temperatures and times depend on the specific powder used and are carefully controlled to ensure proper bonding and curing.
Cooling: After curing, the metal object is allowed to cool down to room temperature. Cooling is essential to prevent any damage or deformation to the freshly coated surface.
Inspection: Finally, the powder-coated metal is inspected for quality and consistency. Any necessary touch-ups or corrections can be made at this stage to ensure a flawless finish.
Key benefits of powder coating as a metal finishing technique:
Enhanced Durability: Powder coating provides a robust and durable finish that is resistant to chipping, scratching, and fading, ensuring the metal product retains its appearance and functionality even under harsh conditions.
Corrosion Resistance: The cured powder coating forms a protective barrier that shields the metal surface from moisture and environmental elements, significantly reducing the risk of corrosion and rust formation.
Aesthetic Versatility: Powder coatings come in a vast array of colors, textures, and finishes, allowing for creative and customizable designs to match any aesthetic requirement or branding needs.
Eco-Friendly: An environmentally friendly metal finishing technique that produces minimal waste and contains no volatile organic compounds (VOCs), reducing air pollution and environmental impact.
Cost-Effectiveness: Due to its high transfer efficiency, minimal material wastage, and reduced energy consumption during curing, resulting in savings for manufacturers and consumers alike.
Silk Screening as a Metal Finishing Technique
Silk screening, also known as screen printing, is a precise and intricate metal finishing technique that allows for the application of detailed designs, patterns, or logos onto metal surfaces. Silk screening offers exceptional versatility and customization options, whether for branding purposes or decorative elements.
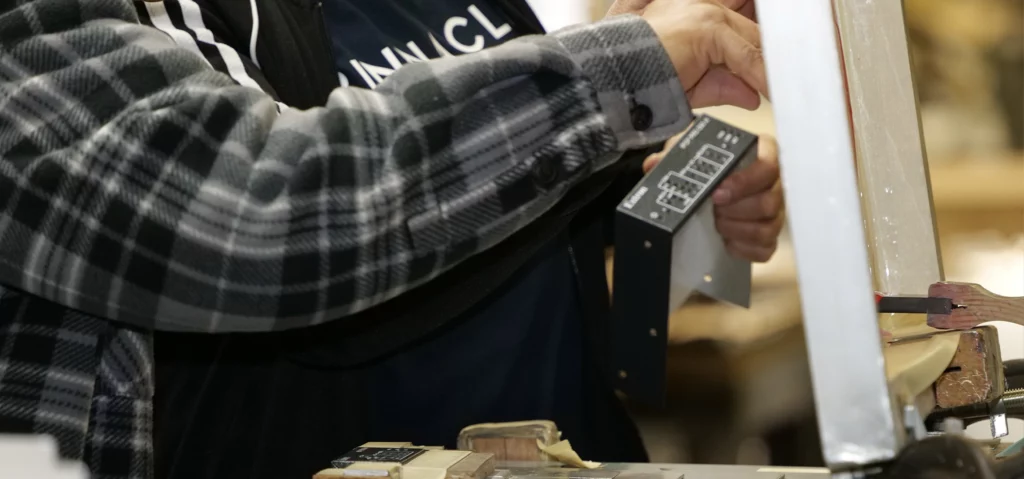
The process of silk screening as a metal finishing technique involves the following steps:
Design Preparation: The first step in silk screening is preparing the design to be printed onto the metal surface. The design is typically created digitally using specialized software, ensuring the desired level of detail and accuracy.
Screen Preparation: A fine mesh screen, usually made of silk or synthetic materials like polyester, is selected based on the intricacy of the design. The screen is coated with a light-sensitive emulsion, and the prepared design is printed onto a transparent film. The film is then placed on the emulsion-coated screen and exposed to ultraviolet light, causing the emulsion to harden and create a stencil of the design on the screen.
Screen Printing Setup: The prepared screen is mounted onto a printing press, with the metal substrate securely positioned below it. The screen is aligned to ensure precise registration of the design onto the metal surface.
Application: Specialized ink for screen printing, often composed of pigments or dyes mixed with a binder, is applied onto the screen. The ink is then spread over the design area using a squeegee, forcing it through the open mesh areas of the stencil and onto the metal below.
Printing Process: The printing press is activated, and the squeegee is pulled across the screen, transferring the ink onto the metal surface in the exact pattern of the design. For multicolor designs, multiple screens with different stencils are used, and each color is applied separately, allowing for precise color registration.
Curing: After the ink is applied to the metal surface, it must be cured to create a permanent bond. The curing process typically involves heating the metal to a specific temperature to ensure the ink dries and adheres securely to the substrate.
Post-Printing Inspection: Once the ink has cured, the metal substrate is inspected to ensure the design is accurately printed and adhered properly. Any necessary touch-ups or corrections can be made at this stage to achieve the desired final result.
Key benefits of silk screening as a metal finishing technique:
Precision and Detail: Silk screening allows for the accurate reproduction of intricate designs, logos, and patterns onto metal surfaces with exceptional detail and clarity, resulting in visually stunning and high-quality finishes.
Versatility: Silk screening is highly versatile and can be applied to a wide range of metal substrates, including steel, aluminum, brass, and more, making it suitable for various industries and applications.
Customization: The flexibility of silk screening enables the customization of metal products to match specific branding, design, or identification requirements, providing a unique and personalized touch to each item.
Durable and Long-Lasting: Screen-printed designs on metal surfaces exhibit excellent durability and resistance to wear, ensuring the artwork remains intact and visually appealing even under harsh conditions.
Cost-Effective for Large Productions: Once the screen is prepared, silk screening becomes a cost-effective method for large-scale production, allowing for efficient and rapid application of designs onto multiple metal items.
Comparing Painting, Powder Coating, and Silk Screening
When comparing Painting, Powder Coating, and Silk Screening as metal finishing techniques, several key differentiators stand out, each offering unique advantages and applications:

Key benefits of silk screening as a metal finishing technique:
Painting: Painting is a relatively straightforward process involving the application of liquid paint to the metal surface. It is versatile, suitable for both simple and complex shapes, and offers a wide range of color and finish options.
Powder Coating: Powder coating involves applying a dry powder to the metal surface, which is then cured to form a durable finish. It requires specific equipment and a curing oven, making it more complex than painting but offers excellent durability, efficiency, and eco-friendliness.
Silk Screening: Silk screening is a precise and intricate process that requires creating stencils and screens for each design. It is best suited for detailed and multicolored artwork, making it ideal for branding, logos, and intricate patterns.
Durability and Performance:
Painting: While painting provides good aesthetic value and moderate protection, its durability may be lower compared to powder coating or silk screening.
Powder Coating: Powder coating offers exceptional durability, corrosion resistance, and abrasion resistance, making it highly suitable for outdoor and industrial applications.
Silk Screening: The ink used in silk screening provides good adhesion and longevity, making the designs resistant to wear and fading, ensuring a long-lasting finish.
Aesthetics and Customization:
Painting: Painting allows for a wide range of colors, textures, and finishes, making it highly customizable and versatile for various decorative applications.
Powder Coating: Powder coating provides a smooth and consistent finish, but its color and texture options may be more limited than painting.
Silk Screening: Silk screening excels in precise and intricate designs, offering exceptional detail and the ability to use multiple colors, making it ideal for branding and customization.
Cost and Efficiency:
Painting: Painting is generally cost-effective and efficient for smaller projects or when a wide range of colors is needed.
Powder Coating: While the initial setup cost for powder coating may be higher, it becomes cost-effective for large-scale production due to its high transfer efficiency and minimal material wastage.
Silk Screening: Silk screening can be cost-effective for medium to large production runs, especially when consistent and detailed designs are required.
Environmental Considerations:
Painting: Water-based paints and low-VOC options make painting a more environmentally friendly choice.
Powder Coating: Powder coating is eco-friendly, producing minimal waste and containing no VOCs, making it a greener option for metal finishing.
Silk Screening: Silk screening also offers eco-friendly options with water-based inks, aligning with environmentally conscious practices.
Confidently Choosing Your Metal Finishing Process and Partner
When it comes to choosing the right metal finishing process, it’s crucial that you understand the end-product requirements and environmental implications before choosing a finishing technique.
You also need to consider the type of metal substrate being used, its compatibility with different finishing techniques, and the desired aesthetics, such as color, texture, and visual effects, to match the intended purpose and design. Cost-effectiveness is crucial, so weigh the initial investment, ongoing maintenance needs, and potential value addition to the end product.
As your proven surface finishing specialists, Pinnacle Precision will help you with all your metal fabrication and finishing needs. Delivering a ‘new level of precision’, they are certified masters of any metal surface and any metal part. Using only industry-leading materials to enhance the strength, durability, and appearance of every part produced here, there’s no one better in the business when it comes to metal finishing.
Talk to the Pinnacle team today for a functional, aesthetic, and valuable metal surface finish.
Experience a new level of precision
The advantages of choosing a local metal fabrication company are undeniable. From improved communication and collaboration to enhanced quality control and timely project completion, the benefits speak for themself. Plus, by opting for a nearby fabricator, you can actively participate in the fabrication process, ensuring that your project is executed to your exact specifications.
Next time you require metal fabrication services, consider the advantages of working with a local company like Pinnacle. With a focus on delivering high-quality, on-time parts, we take the time and care to precisely understand what you need as a customer to solve your specific challenges.
Contact us today for a quote.