In a high-risk, high-intensity medical environment, precision isn’t just important; it’s critical. To ensure patient safety and procedural success, every device, component, and tool must meet rigorous performance, safety, and hygiene standards. With so much at stake, even the slightest deviation in a dimension compromises the outcome. That’s why CNC (Computer Numerical Control) machining has become an essential manufacturing method for medical components.
CNC machining offers the accuracy, repeatability, and material versatility required to produce precision parts for a wide range of critical medical devices, surgical equipment, diagnostics systems, and facility installations. It supports the production of everything from one-off custom prosthetics to complex assemblies used in high-tech diagnostic machines.
For over 50 years, Pinnacle Precision has been a trusted partner to the medical industry, precision machining medical parts that meet the highest standards of accuracy and performance. Our Technical, Production, and Quality Assurance teams bring decades of experience to every project, ensuring that every component, bracket, enclosure, or frame is meticulously crafted to serve its purpose in life-saving technologies.
In this article, we explore the key medical applications of precision CNC-machined parts, the main benefits of this manufacturing method, and the reasons why Pinnacle is the trusted partner for medical CNC machining.
Top 5 CNC Machining Applications in Medical Manufacturing
While CNC machining plays a role across a wide range of medical applications, five categories stand out for their impact, complexity, and relevance in modern healthcare systems. These applications highlight the importance of machining for the medical field, where precision, consistency, and patient safety are paramount.
Equipment Carts & Workstations
Whether it’s a surgical suite, mobile diagnostic unit, or hospital laboratory, equipment carts, and workstations play a critical role in supporting daily operations. These mobile units must be ergonomic, durable, and adaptable to different clinical environments.
CNC machining processes enable the production of:
- Custom drawer systems
- Telescoping support arms
- Mobile workstation frames
- Precision-fit joints and connections
By using biocompatible materials such as stainless steel, aluminum, and medical-grade composites, Pinnacle Precision manufactures carts that are not only strong and lightweight but also easy to clean and corrosion-resistant, vital for maintaining sterile environments. When it comes to medical equipment that supports minimally invasive surgeries or lab diagnostics, our advanced technologies ensure that each moving part operates with fluid precision and reliability, supporting clinicians and technicians throughout their workflows.
Brackets & Mounts
In the medical world, everything needs to be mounted securely, whether it’s a patient monitoring system, imaging screen, IV pump, or surgical light. CNC-machined brackets and mounts are the unsung heroes that keep critical equipment safely in place, often supporting orthopedic devices, surgical instruments, and specialized medical equipment.
Precision CNC machining allows for:
- Complex geometries and hole patterns
- Load-bearing design
- High corrosion resistance for wash-down areas
- Custom fits for proprietary devices
At Pinnacle Precision, we manufacture these support components using customer specified materials like aluminum, titanium, stainless steel, and medical-grade aluminum alloys to ensure long-term durability and compliance in medical device manufacturing. Our engineers collaborate with OEMs to develop high-performance bracketry that integrates seamlessly with larger assemblies used in labs, operating rooms, and recovery areas.
Enclosures & Housings
Sensitive electronics and medical instruments must be protected from environmental factors like moisture, contaminants, and electromagnetic interference (EMI). CNC-machined enclosures and housings serve as durable, protective barriers, ensuring diagnostic and monitoring devices function reliably under demanding real-world medical conditions.
Common CNC-machined housings include:
- Monitor and control panel cases
- Diagnostic imaging equipment shells
- Respirator and ventilator component covers
- EMI-shielded enclosures for sensitive electronics
At Pinnacle Precision, we manufacture high-tolerance enclosures from Medical Grade materials like titanium, aluminum and stainless steel, incorporating tapped holes, cooling fins, ports, or gaskets for specific applications. These enclosures often house components for minimally invasive surgeries and medical implants, where shielding and sterility are crucial. Our post-machining capabilities, such as powder coating, anodizing, and antimicrobial treatments, further support long-term patient safety and regulatory compliance.
Structural Frames
The backbone of many laboratory and diagnostic systems lies in their structural frames. These large, high-precision assemblies support a variety of devices and instruments used in testing, imaging, and research.
Structural frame machining requires:
- Flatness and squareness across large dimensions
- High-strength materials with low vibration
- Precise hole alignment and spacing
- Modular design integration
With extensive experience in medical machining, the team at Pinnacle produces structural frames used in medical device manufacturing, ensuring consistency and accuracy across every weldment and support element. Our CNC machining capabilities support the production of components for medical devices designed for human body interfaces or implant integration. These frames are critical to the reliability and performance of some of the most advanced medical equipment today.
Custom Fixtures & Hardware
In hospitals, surgical centers, and R&D labs, specialized fixtures and hardware are often required to support specialized installations, prototypes, or next-generation medical devices. Components like these are often used in or around surgical tools, imaging systems, and other custom clinical applications.
Custom CNC-machined fixtures and hardware include:
- Control panels
- Instrument handles and knobs
- Base plates for wall or ceiling mounting
- Custom mechanical interfaces
Pinnacle Precision manufactures these precise components using a wide range of biocompatible materials, including titanium, Delrin®, and stainless steel. Whether supporting orthopedic devices, facilitating minimally invasive procedures, or housing interface elements for advanced diagnostic systems, our CNC machining solutions are built for the demands of the medical field. With in-house secondary operations, including hardware installation, gasketing, and finishing, our team ensures each part is production-ready and aligned with function and form.
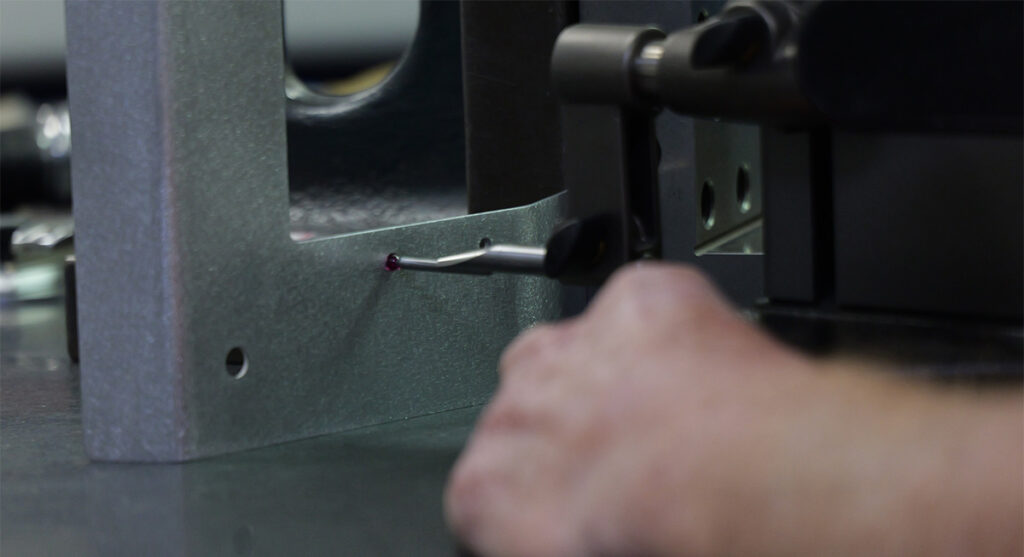
Benefits of CNC Machining for Medical Components
CNC machining offers unique advantages to the medical industry, enabling precise fabrication of surgical instruments, diagnostic devices, and life-saving equipment. Its ability to achieve tight tolerances, complex shapes, and repeatable accuracy is essential for producing high-performance surgical tools that must perform flawlessly during critical medical procedures.
From rapid prototyping to full-scale medical device development, the additive manufacturing method supports every phase of innovation. As a cornerstone of modern medical machining, it ensures the production of safe, sterile, and highly reliable components that meet strict regulatory and functional requirements and improve patient recovery.
Tight Tolerances for Critical Applications
Medical components must meet tight tolerances to ensure accurate readings, secure fits, and smooth performance. CNC machining enables sub-millimeter precision with excellent repeatability, which is critical for implants, enclosures, and structural assemblies.
Material Versatility
Material versatility is a critical advantage of CNC machining for medical components, allowing manufacturers to select from a wide range of biocompatible materials like titanium, stainless steel, aluminum, and medical-grade plastics.
This flexibility supports the production of medical implants, surgical instruments, diagnostic equipment, and orthopedic devices that must meet strict patient safety standards while maintaining durability, corrosion resistance, and high strength.
Pinnacle Precision is an expert at working with a wide array of medical-grade materials, including:
- Titanium – Lightweight, strong, and biocompatible; ideal for orthopedic and implantable devices.
- Stainless Steel – Durable and corrosion-resistant; widely used for tools, brackets, and housings.
- Aluminum – Lightweight and cost-effective; used in carts, enclosures, and structural parts.
- Medical Plastics – Including PEEK and Delrin® for non-metallic, non-conductive components.
Our experience with diverse materials ensures proper handling, machining parameters, and finishing processes for medical-grade requirements.
Scalability for Prototypes and Full Production
Whether you’re developing a one-off prototype for a new diagnostic system or need thousands of identical housings for a product launch, CNC machining offers the scalability and speed to match.
Pinnacle Precision offers:
- Rapid prototyping with short lead times
- Small-to-medium batch runs with consistent quality
- Full-scale production supported by strict quality assurance
Our Technical and Production teams leverage the power and accuracy of CNC machines to deliver the high quality and consistency demanded in the medical industry.
Our continued investment in the latest CNC tools, including a large 5-axis machine, enables us to meet the most stringent quality standards while ensuring efficient and cost-effective production processes of complex metal parts and components.
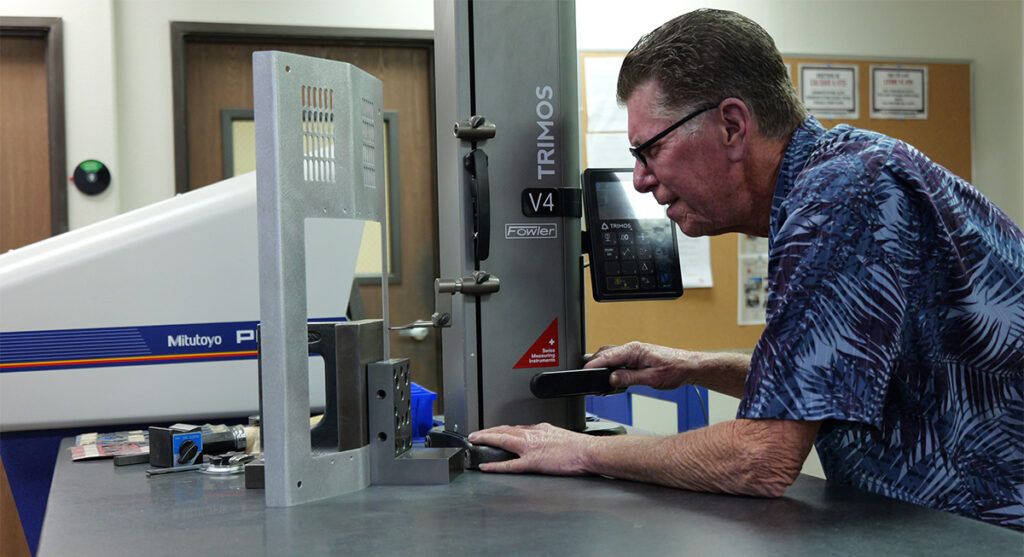
Why Pinnacle Precision is a Trusted CNC Partner for Machining Medical Parts
With patients’ health and safety on the line, medical manufacturers need to know they’re working with a team relentlessly committed to precision, performance, and reliability. Over the last 50 years, we have delivered unrivaled quality in the production of cutting-edge medical devices that require exacting standards to protect patients and ensure reliability.
Our capabilities empower the industry with innovative solutions that drive progress and improve patient care.
CNC Machining Expertise Backed by Collaboration
Our CNC machining teams specialize in transforming complex 3D models into fully machined parts that meet exacting standards. But we go beyond machining. We engage in early-stage planning, provide DFM (Design for Manufacturability) feedback, and work alongside engineering teams to reduce costs and enhance performance.
Cutting-Edge Technology for Demanding Applications
Our 73,000-square-foot facility is equipped with:
- Multi-axis CNC machines
- Automated pallet systems
- Precision measuring tools and inspection stations
- Lights out Manufacturing
This infrastructure enables us to machine complex geometries while maintaining consistency, quality, and efficiency.
End-to-End Capabilities That Save Time and Reduce Risk
Our integrated services help medical manufacturers streamline supply chains.
We provide:
- Material sourcing and traceability documentation
- Secondary operations (welding, hardware installation, gasketing)
- Quality control to ISO 9001, AS9100D and customer-specific standards
- Final assembly and packaging for shipment
- In-house finishes, paint and powder coat
We’ve helped customers manufacture everything from ventilator frames to surgical housings with complete confidence in fit, function, and cleanliness.
How Pinnacle Ensures Compliance with Standards for Medical Applications
When performance is a matter of life and death, compliance with strict medical regulations is not a choice; it’s a non-negotiable. Here at Pinnacle, we take safety seriously and are fully committed to maintaining the highest standards in the industry.
With a robust quality management system in place, we ensure adherence to key standards and FDA requirements, guaranteeing that every part we produce meets stringent safety and quality guidelines.
Our robust quality control measures include:
- Multi-Stage Inspections: From the initial design to final production, we conduct strict inspections and testing at every stage of the manufacturing process to catch any potential defects early.
- Precision Measuring Tools: We use advanced tools like Coordinate Measuring Machines (CMM) and laser to ensure every part we produce meets the exact specifications required.
- Material Traceability: We maintain full material traceability and documentation, ensuring all components meet regulatory standards and allowing for seamless reporting when needed.
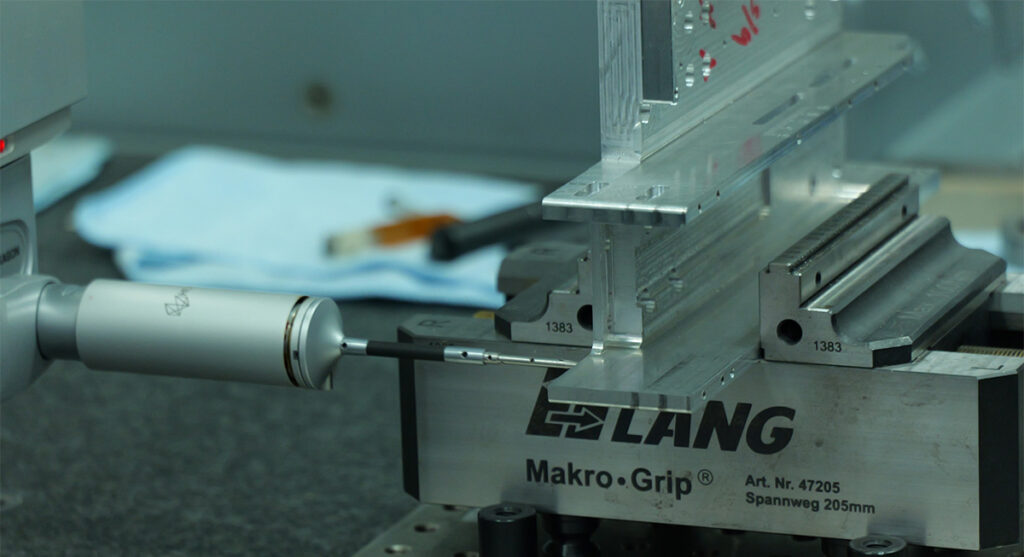
CNC Machining’s Role in Advancing Healthcare
As medical devices become smarter, smaller, and more integrated into patient care, the demand for high-precision manufacturing grows. CNC machining continues to be a critical enabler of medical innovation, offering the control, speed, and scalability that today’s technologies require.
From creating secure frames for laboratory analyzers to manufacturing mobile workstations for intensive care units, CNC machining underpins some of the most essential equipment in modern medicine. Its unmatched precision supports better outcomes, smoother workflows, and improved device longevity.
At Pinnacle Precision, we’re more than just a CNC shop; we’re a partner in delivering life-saving technologies. Whether you need help developing a new prototype, scaling production, or solving a manufacturing challenge, our team is here to collaborate and deliver solutions.